Inventory replenishment is the cornerstone of efficient warehouse operations. It ensures that stock levels are maintained at optimal levels to meet customer demand, avoid stockouts, and reduce overstocking. In the modern supply chain landscape, traditional replenishment methods are being enhanced by cutting-edge technologies like Artificial Intelligence (AI), Machine Learning (ML), and automation tools such as Autonomous Mobile Robots (AMRs) and Automated Storage and Retrieval Systems (AS/RS). These advanced systems not only streamline replenishment but also increase accuracy and operational efficiency.
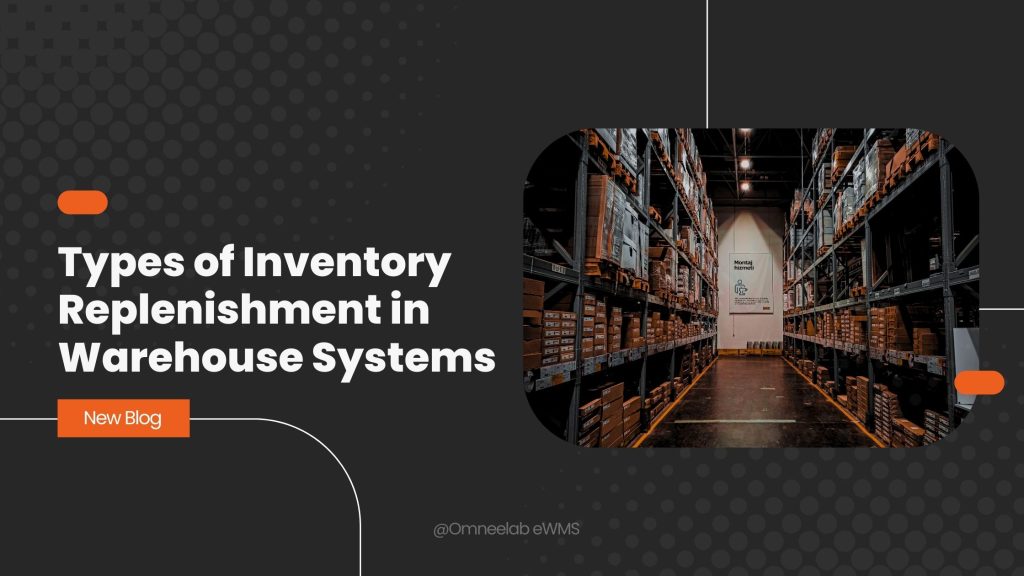
In this article, we’ll discuss the different types of inventory replenishment methods used in warehouse systems, ranging from traditional approaches like Min/Max Inventory Replenishment to advanced technology-driven solutions. We’ll also explore how AI, ML, and IoT are transforming inventory management, providing insights into how warehouses can adopt these methods to stay competitive.
Understanding Inventory Replenishment in Warehouses
Inventory replenishment involves moving stock from reserve storage areas to picking locations or placing orders with suppliers to replenish inventory levels when they fall below a certain threshold. The goal is to ensure that products are available when needed while minimizing holding costs.
Modern inventory replenishment focuses on efficiency, accuracy, and cost-effectiveness by leveraging advanced tools and technologies. From traditional time-tested methods to futuristic automation systems, replenishment strategies vary depending on the business model, demand patterns, and technological adoption.
Types of Inventory Replenishment in Warehouse Systems
1. Min/Max Inventory Replenishment
Min/Max replenishment is one of the most widely used traditional inventory methods. It works by setting a minimum stock level (the reorder point) and a maximum level (the desired inventory level after replenishment). When inventory falls below the minimum threshold, a replenishment order is triggered to bring the stock back up to the maximum level.
- Best For: Items with consistent demand.
- Key Advantage: Simplicity and ease of implementation.
- Limitation: Requires regular monitoring and may not adapt well to fluctuating demand.
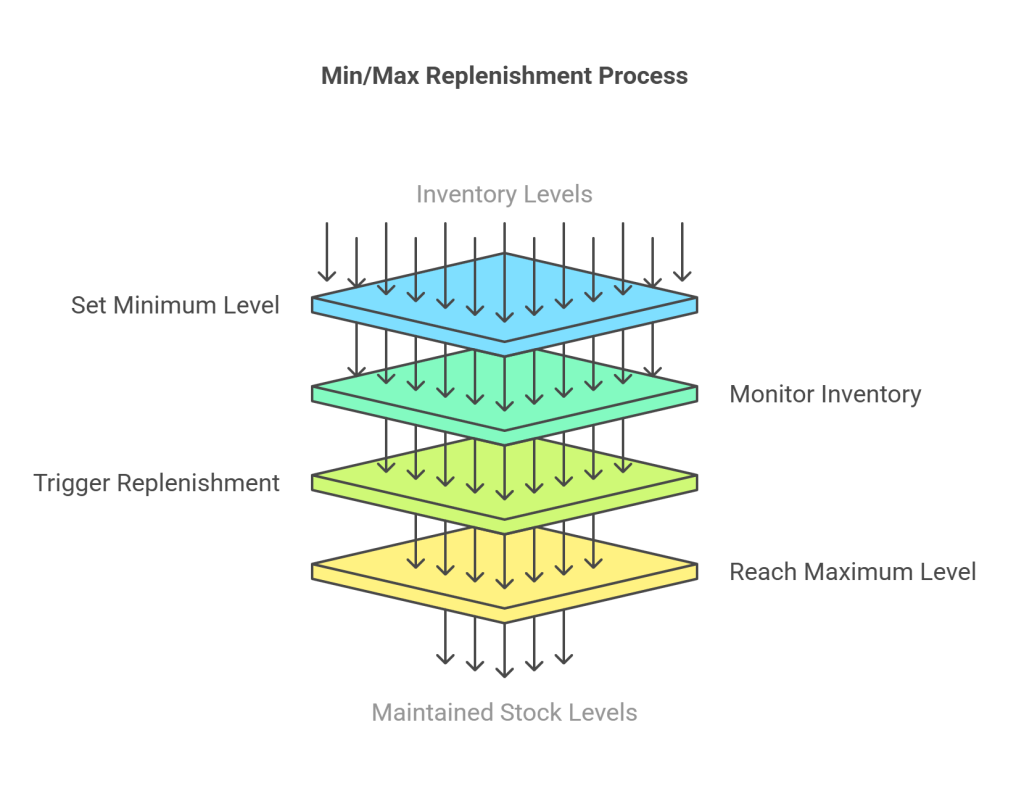
2. Demand Inventory Replenishment
Demand-based replenishment focuses on real-time consumption and sales data to trigger replenishment. Instead of relying on static thresholds, this method dynamically adjusts replenishment based on actual product demand.
- Best For: Products with highly variable demand.
- Key Advantage: Reduces overstock and stockouts by aligning inventory levels with real-time demand.
- Technology Integration: Often supported by AI and ML for demand forecasting.
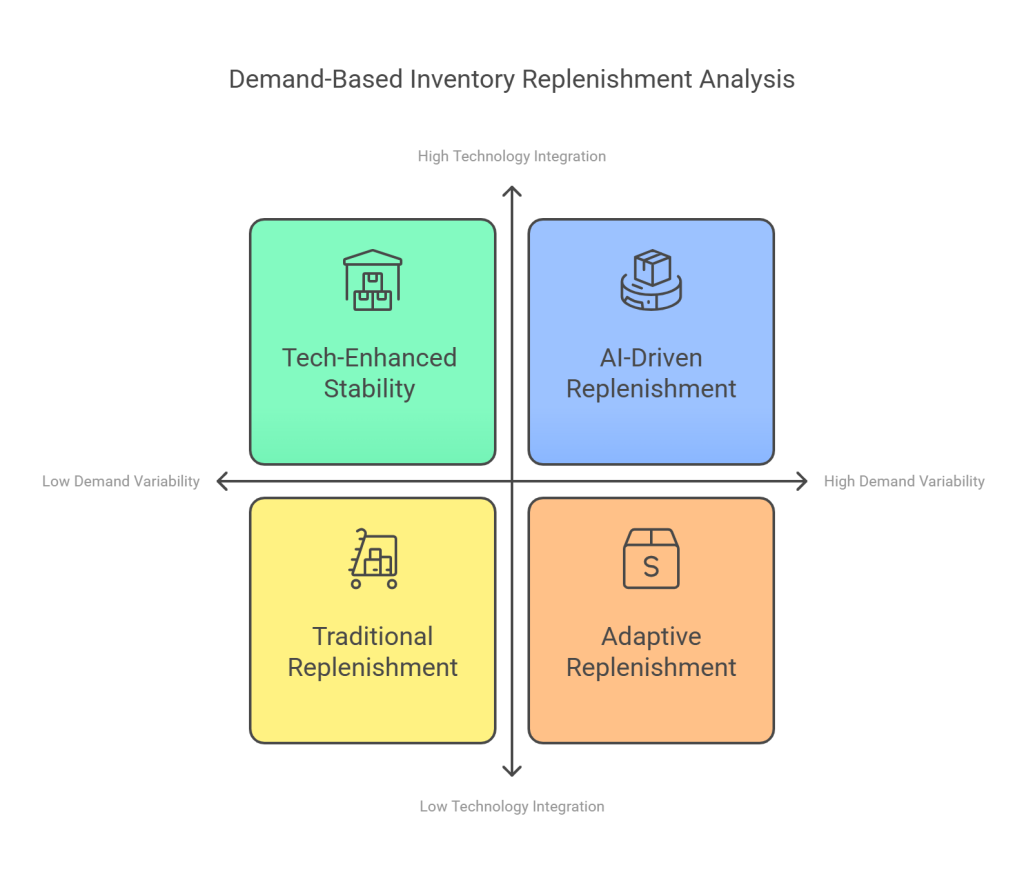
3. Top-Off Inventory Replenishment
Top-off replenishment is a proactive method where inventory levels in picking locations are replenished before they run out. This method is commonly used during off-peak times to ensure that picking operations run smoothly during peak hours.
- Best For: High-volume warehouses with frequent order picking.
- Key Advantage: Prevents disruptions in order fulfillment by preemptively replenishing stock.
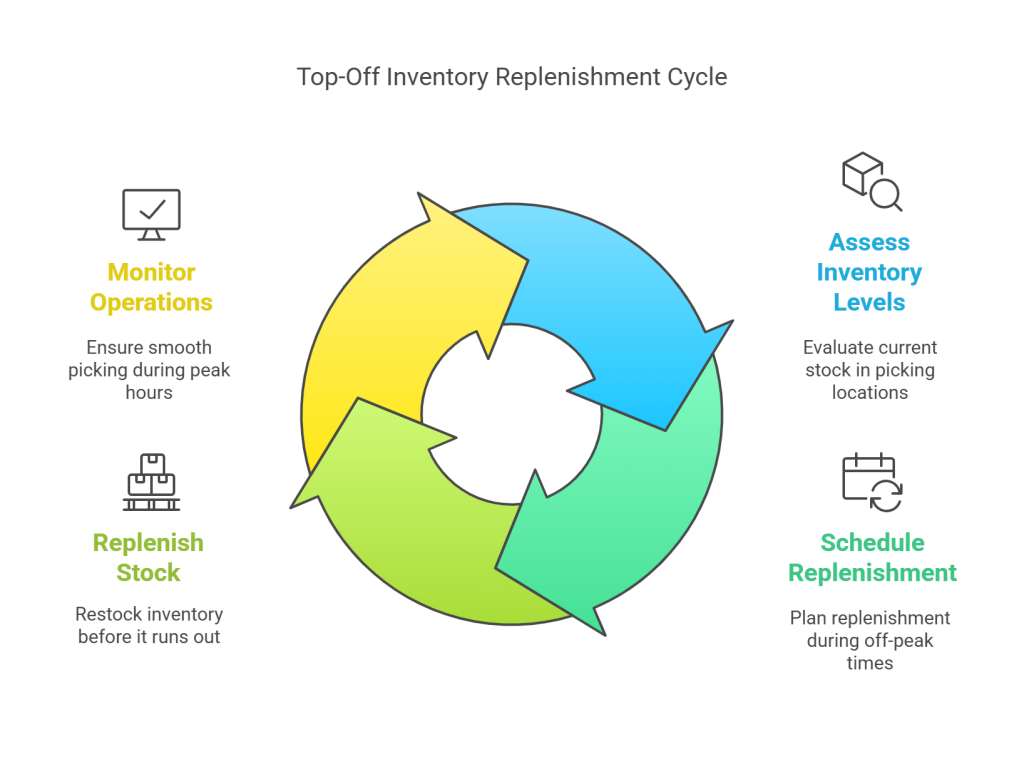
4. Periodic Inventory Replenishment
In periodic replenishment, inventory levels are reviewed and replenished at fixed intervals, regardless of demand. This method is often used for products with predictable demand patterns or when managing inventory across multiple locations.
- Best For: Businesses with stable and predictable demand.
- Key Advantage: Simplifies inventory management by aligning replenishment with accounting cycles.
- Limitation: May result in stockouts or overstocking if demand fluctuates significantly.
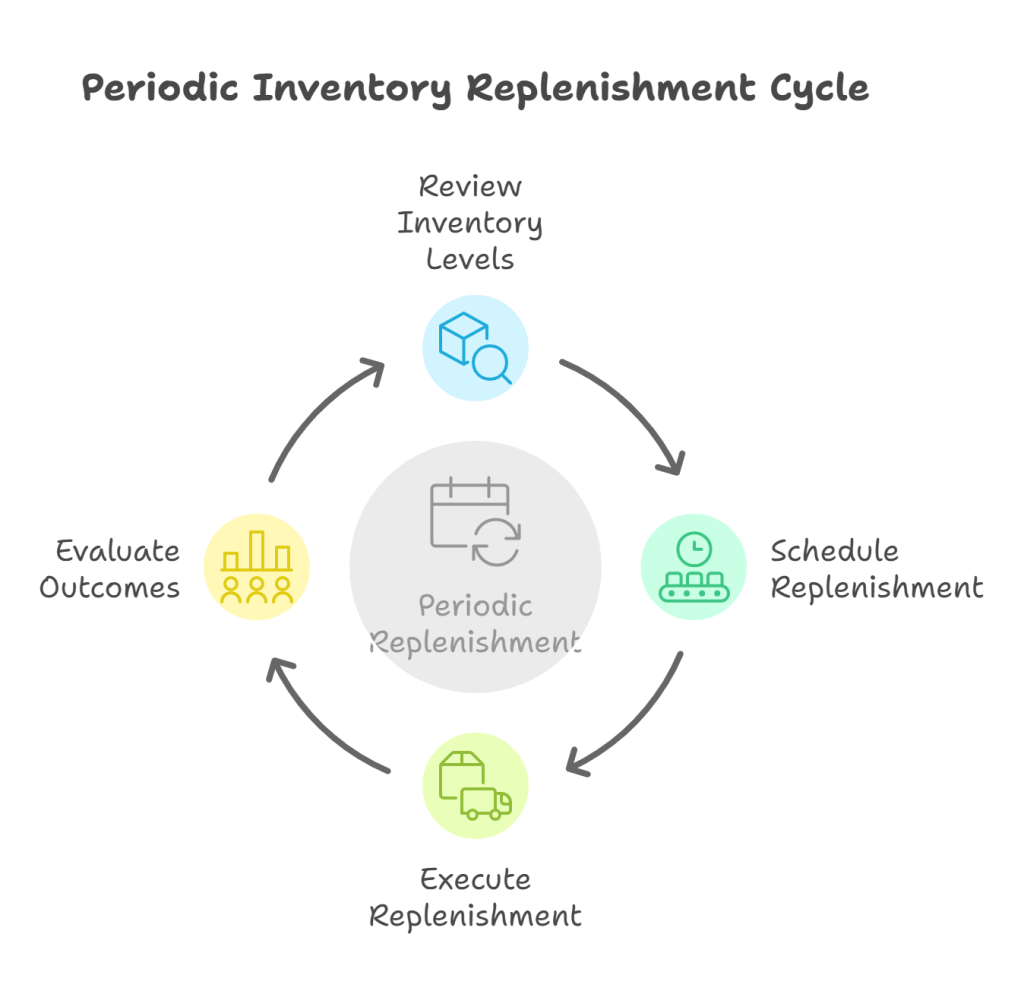
5. Economic Order Quantity (EOQ)
EOQ is a mathematical approach to inventory replenishment that determines the optimal order quantity by balancing ordering costs and holding costs. It is designed to minimize the total cost of inventory management.
- Best For: Businesses looking to optimize costs.
- Key Advantage: Reduces total inventory costs while maintaining adequate stock levels.
- Limitation: Requires accurate cost and demand data for effective implementation.
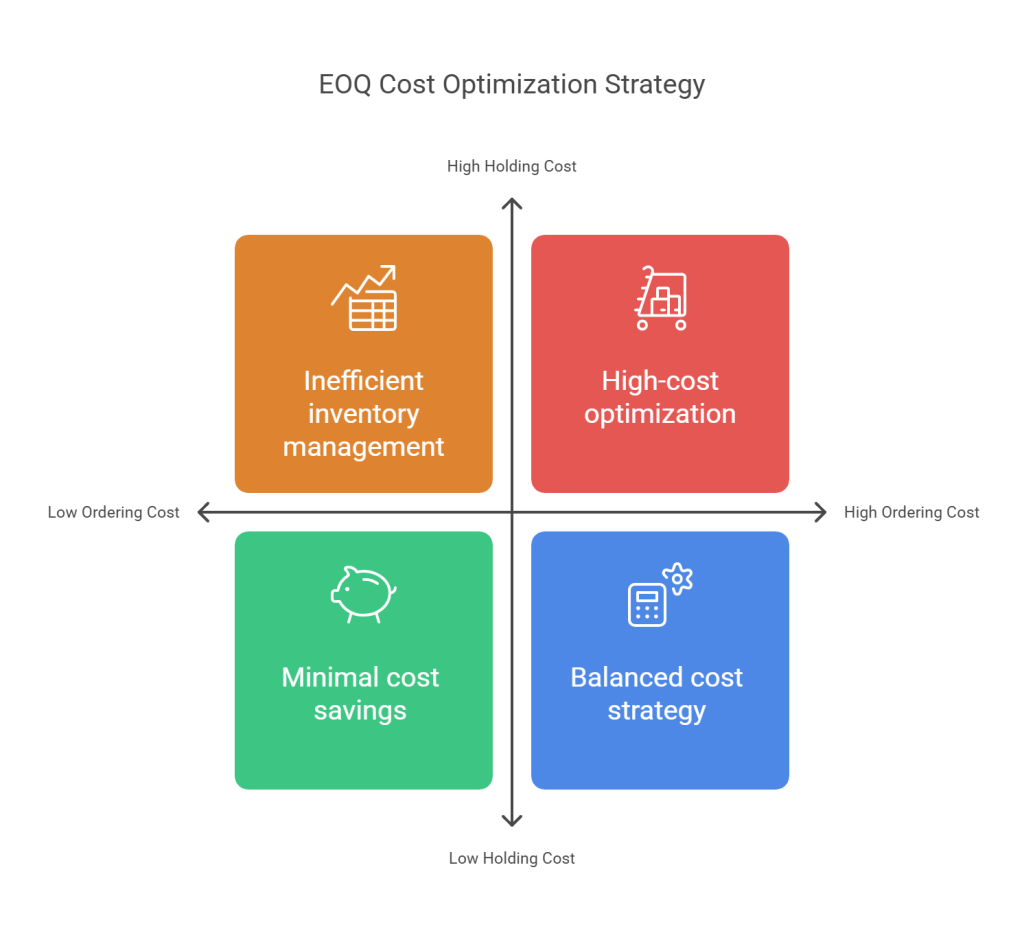
Technology-Driven Replenishment Solutions
As warehouses scale operations and customer expectations increase, traditional replenishment methods alone may fall short. Technology-driven replenishment solutions offer unparalleled efficiency, accuracy, and scalability.
Automated Storage and Retrieval Systems (AS/RS)
AS/RS are highly automated systems that use robotics to store and retrieve inventory. These systems are particularly effective in warehouses with high storage density requirements.
Best For: Warehouses with high SKU (Stock Keeping Unit) counts.
Key Features:
- Maximizes use of vertical space.
- Reduces picking errors and labor costs.
- Improves operational efficiency.
Autonomous Mobile Robots (AMRs)
AMRs are technologically advanced robots that navigate warehouse floors autonomously to transport inventory. They play a critical role in automating replenishment by moving stock from storage to picking areas.
Best For: Large warehouses with high order volumes.
Key Features:
- Real-time inventory tracking.
- Flexible routing capabilities.
- Enhanced safety and efficiency.
Artificial Intelligence (AI) and Machine Learning (ML)
AI and ML are transforming inventory replenishment by enabling predictive analytics and intelligent decision-making. These technologies analyze historical data, current trends, and external factors to forecast demand and optimize replenishment schedules.
Key Benefits:
- Accurate demand forecasting.
- Reduced stockouts and overstocking.
- Improved decision-making for replenishment and procurement.
Internet of Things (IoT) Integration
IoT devices, such as smart sensors and RFID tags, enable real-time inventory tracking and monitoring. They provide valuable data on stock levels, product movement, and environmental conditions.
Key Benefits:
- Improved supply chain visibility.
- Automated stock level updates.
- Real-time alerts for stock replenishment needs.
Choosing the Right Replenishment Strategy
Selecting the right inventory replenishment method depends on various factors, including business size, product characteristics, and demand patterns. Here are some steps to determine the best strategy:
Assess Your Business Needs
- Identify the nature of your products (e.g., perishable, non-perishable).
- Analyze demand variability and predictability.
Leverage Technology
- Use AI and ML tools for demand forecasting.
- Implement IoT devices for real-time tracking.
Integrate Systems
- Ensure seamless integration between Warehouse Management Systems (WMS), Enterprise Resource Planning (ERP) systems, and inventory management software.
Future Trends in Inventory Replenishment
The future of inventory replenishment lies in automation, data-driven decision-making, and advanced supply chain visibility. Here are some trends to watch:
- Blockchain Technology: Enhances transparency and traceability in inventory management.
- Smart Warehouses: Fully automated warehouses integrating AI, IoT, and robotics.
- Sustainability Initiatives: Reducing waste and optimizing inventory to meet environmental goals.
Conclusion
Inventory replenishment is no longer just about maintaining stock levels; it has become a strategic function that drives operational efficiency, customer satisfaction, and cost optimization. From traditional methods like Min/Max replenishment to advanced solutions leveraging AI, ML, and IoT, businesses have a variety of options to choose from based on their unique needs.
The integration of automation tools like AMRs, AS/RS, and predictive analytics ensures that replenishment systems are not only accurate but also scalable for growing business demands. As technology continues to evolve, warehouses that embrace innovative replenishment strategies will gain a competitive edge in the market.
Are you ready to revolutionize your warehouse operations? Explore AI-powered inventory replenishment tools to optimize your stock levels and improve efficiency. Contact Omneelab eWMS today to learn how advanced warehouse automation can transform your business.
FAQs
Inventory optimization involves managing stock levels to meet customer demand while minimizing costs. It ensures that warehouses maintain the right amount of stock—avoiding overstocking and stockouts. By leveraging tools like AI, ML, and IoT, businesses can forecast demand, reduce holding costs, and improve overall operational efficiency.
Demand forecasting uses historical data, market trends, and AI-powered algorithms to predict future demand accurately. This allows businesses to replenish inventory proactively, reducing the risk of running out of stock or holding excess inventory. Accurate forecasts are key to aligning replenishment strategies with actual customer needs and improving supply chain visibility.
Safety stock is a buffer inventory maintained to account for unexpected fluctuations in demand or supply chain disruptions. It ensures that warehouses can meet customer orders even during unforeseen circumstances. Managing safety stock effectively requires tools like Warehouse Management Systems (WMS) and real-time inventory tracking to balance holding costs and service levels.
IoT devices and RFID technology enable real-time tracking of inventory by collecting and transmitting data about stock levels, product movement, and storage conditions. This enhances supply chain visibility and ensures timely replenishment. For instance, smart sensors can send alerts when inventory levels fall below a critical threshold, triggering automated reordering systems.
Periodic replenishment occurs at fixed intervals, regardless of current stock levels, making it ideal for products with predictable demand. On the other hand, top-off replenishment is a proactive approach where stock is refilled before it runs out, often during off-peak hours. Top-off replenishment is commonly used in high-volume warehouses to ensure smooth order fulfillment during peak times.
Kapil Pathak is a Senior Digital Marketing Executive with over four years of experience specializing in the logistics and supply chain industry. His expertise spans digital strategy, search engine optimization (SEO), search engine marketing (SEM), and multi-channel campaign management. He has a proven track record of developing initiatives that increase brand visibility, generate qualified leads, and drive growth for D2c & B2B technology companies.