If you’re a small business and considering the benefits of the barcode tracking system, keep reading because you will learn that it is not only for the big boys. Maximize your minuscule investment in a small business barcode tracking and inventory management system and discover how to slash those costly, time-consuming stock takes in half. To begin, let’s recap the idea of the small business barcoding tracking system.
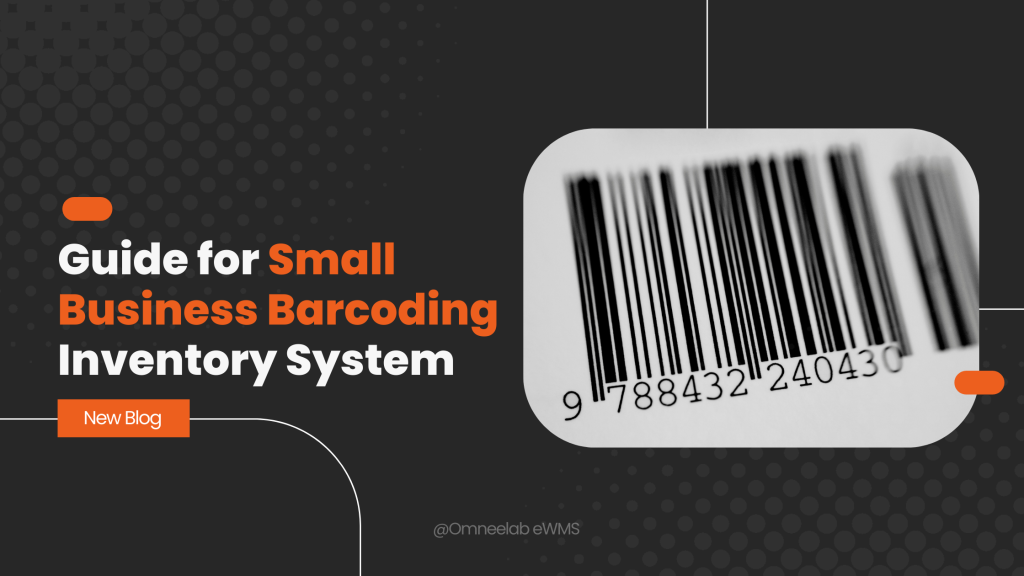
Find out how using small business barcode software can help you manage your inventory better. In this guide, you will learn setup tips, advantages, and software to manage your stock effectively.
Barcode Tracking Matters for Small Businesses
Hello, small business owner! Are you tired of dealing with lost inventory, time-consuming stock takes, or costly mistakes? If so, you’re not alone. Managing inventory can feel like juggling flaming torches—one wrong move, and everything can come crashing down. But don’t worry, there’s a solution: small business barcode tracking. It’s a simple, affordable way to bring order to the chaos of small business inventory management.
In this post, we’ll explore how a barcode inventory system can revolutionize your business operations. From setting up your first system to achieving inventory accuracy, we’ll guide you through the process. Whether you run a retail shop, a small warehouse, a mail-order company, or an online store, barcode tracking is the tool you need to streamline your operations and reduce errors.
So, grab a coffee, and let’s dive into how barcode tracking can make your business run smoother and more efficiently!
What is Small Business Barcoding Tracking?
Before we dive deeper, let’s first demystify what small business barcode tracking really means. At its core, it’s a method of using barcodes—those familiar black-and-white striped labels—to organize and track your inventory. Each barcode represents a unique product, and with just a quick scan, you can instantly access important details like stock levels, sales data, or even product locations.
Think of it as a library card system for your business. Just as librarians scan books to see who’s borrowed what, a barcode inventory system gives you real-time insight into what’s in stock, what’s been sold, and what needs reordering. For small business owners, this isn’t just a fancy gadget—it’s a critical tool for small business inventory management. Say goodbye to guesswork, late-night calculations, and stock discrepancies, and say hello to a streamlined, efficient, and stress-free way of running your business!
The Importance of Barcode Inventory Systems for Small Businesses
So why should you concern yourself with barcode inventory control? Let’s paint a picture. Pretend you own a small boutique. A customer requests a shirt size, but you’re not sure if it’s in stock. You search through boxes, waste 20 minutes, and — whoops — it’s sold out. Frustrating, right? Now, imagine scanning a barcode and knowing the depth of your stock. That’s what inventory tracking does for the small business.
There are many reasons why you should have barcode systems in place:
- Precision: No more human errors in small business stock control. Scans don’t lie.
- Saves Time: No more hand-counting—scanning your warehouse for inventory as quickly as possible.
- Only pay For the Quantity You Need: Do not overbuy or underbuy; save money in the long run.
- Scalability: An automated inventory system scales as your business scales.

Advantages of Barcode Tracking for Small Business Owners
So, let’s talk about the benefits of small business barcode tracking. I’ve witnessed firsthand what it can do to transform a chaotic operation into a well-oiled machine. One of my friends, Sarah, has a tiny craft supply shop. Before she used barcode tracking, she would spend hours counting stock by hand. After setting up a barcode inventory system, she reduced that time by half and even discovered a few thefts she’d overlooked the first time around. Here’s what you can expect:
Real-Time Inventory Updates
Barcode inventory control, where every scan updates stock levels directly. Sold an item? You can scan it, and your system will show the new version. This real-time information is a stock-tracker game changer for small businesses.
Reduced Errors
Manual entries are prone to errors — typos, miscounts, you name it. With a bar code system, this headache is removed, and the process is automatic. Think of it as the nearly perfect assistant who never gets tired.

Better Customer Satisfaction
You can answer the question fairly well when stock is tracked for small businesses through an inventory process. So much for the “Let me see if it’s in the back” excuse!
Better Decision-Making
Having data from a barcode inventory system allows you to identify trends. What products are stalking the empty shelves? Time to reorder. Are others gathering dust? Perhaps it’s time for a markdown.
How to Set Up a Barcode System: A Step-by-Step Guide
Once you are sold on the big picture, let’s discuss how to set up a barcode system for your small business. Don’t worry — it’s not as confusing as it seems. Take Homework out of Homework Any of these options can help students begin to see the value in doing Homework.
Step 1: Assess Your Needs
Figure out what you’re tracking. First, you need to determine what you’re monitoring. Do you run products in retail, stored in the basement, attic, or warehouse? This will inform the tools you need for small business asset tracking.
Step 2: Select the Proper Gear
For scanning barcodes for inventory, here’s what you’ll need:
- The Barcode Scanner is handheld or fixed to your surface.
- Barcode Printer: This is for businesses that need to generate barcodes for their products.
- Software: Choose a platform that is easy to use and that syncs with your sales system.
Step 3: Generate Barcodes
Generate unique barcodes for individual products using software or online services. Print them with a label maker for crisp, scannable tags. This forms part of good control of inventory in a bag with a barcode.
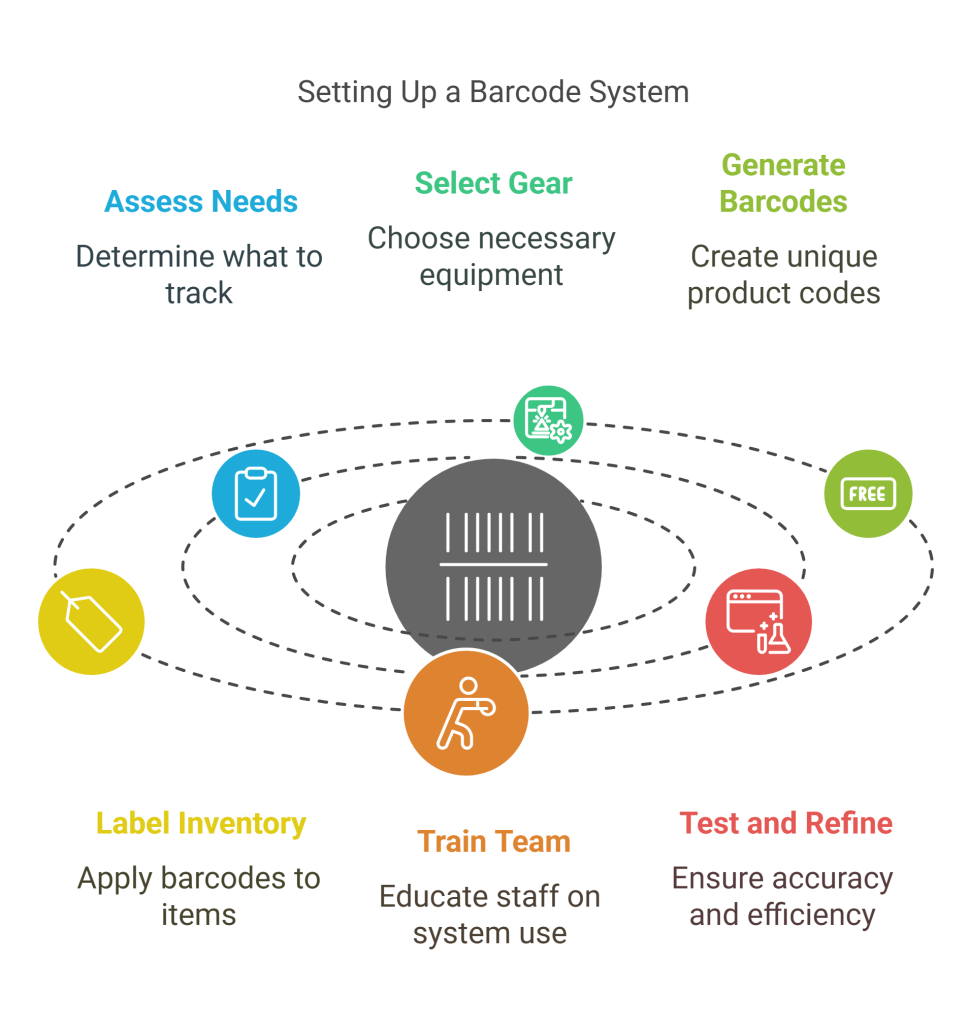
Step 4: Label Your Inventory
Slap those barcodes on your merchandise or shelves. Make the scannable — don’t hide them in weird places!
Step 5: Train Your Team
Train your crew on how to utilize the automated inventory system. A brief demonstration of scanning and updating stock will keep everyone on the same page in the realm of small business stock management.
Step 6: Test and Refine
Conduct a trial to work out kinks. Scan items, ring up sales, and see if your figures match reality. Tweak as necessary to optimize your small business inventory tracking.
Selecting the best/best barcode inventory system for your company
All barcode systems are not equivalent. When selecting a barcode scanner for small business barcode tracking, take these things into account:
- Budget: Seek out budget-friendly options. A lot of cloud-based systems have free trials for small business inventory management.
- Usability: You shouldn’t have to have a tech degree to run a point-of-sale inventory system. Choose intuitive software.
- Integration: Make sure it is compatible with your POS or accounting software to facilitate tracking of products in small businesses.
- Support: Choose providers that offer strong customer support. The last thing you want is to be stranded when the glitch comes to call.
For a top-notch solution, check out OmneelabWMS, a powerful warehouse management system designed to streamline small business barcode tracking. It integrates seamlessly with your operations, offering real-time tracking and user-friendly features to elevate your small business stock tracking. Do your research—read reviews or ask other business owners for referrals.
Common Challenges in Implementing Barcode Systems (And How to Overcome Them)
Let’s face it—not every barcode system implementation goes smoothly. While barcode systems can revolutionize inventory management for small businesses, there are a few common pitfalls that can arise during the rollout process. Here’s a breakdown of the typical challenges you might encounter when introducing barcode tracking systems and how to effectively address them.
Challenge 1: High Initial Costs
Implementing a barcode inventory system can seem expensive, especially if you’re unsure about the equipment and software required. Many small businesses overestimate the costs or invest in overly complex systems that don’t align with their needs.
Solution:
Start small. Invest in a basic barcode scanner and free or low-cost software to get started. As your business grows and you see returns on your investment, you can scale up to more advanced systems with additional features. This phased approach minimizes upfront costs while still allowing you to reap the benefits of barcode inventory control.
Challenge 2: Resistance from Staff
Introducing a new automated inventory system can sometimes be met with resistance from employees. Workers may feel overwhelmed by the learning curve or hesitant to adopt new technology, especially if they’re accustomed to manual processes.
Solution:
Focus on the benefits. Highlight how the system will save time, reduce errors, and make their jobs easier. Provide hands-on training sessions to familiarize your team with the new tools. When employees see how barcode scanning for inventory simplifies their tasks, they’ll be more likely to embrace the change.
Challenge 3: Technical Glitches
Technology isn’t foolproof. Barcode scanners can malfunction, software may freeze, or connectivity issues might disrupt operations. These hiccups can slow down your inventory tracking for small business and create frustration.
Solution:
Prepare for the unexpected. Always maintain backups of your inventory data to prevent loss during technical failures. Additionally, have a manual process in place as a fallback option. Regularly update your software and perform maintenance on your hardware to minimize the risk of breakdowns. Partnering with a reliable barcode system provider can also ensure you have access to technical support when needed.
How to Effectively Manage Small Business Inventory with Barcodes
Managing small business inventory management can seem overwhelming—especially when barcodes are involved—but it’s simpler than you think! With the right strategies and tools, you can streamline your small business stock management and make your operations more efficient. Here are some expert tips to help you maximize your barcode inventory control:
1. Conduct Regular Audits
Even if you’re using an automated inventory system, it’s essential to conduct periodic stock audits. This ensures your data remains accurate and helps you identify discrepancies early. Barcode systems make audits faster and more precise, but human oversight is still crucial to maintaining accuracy.
2. Organize Your Space Efficiently
Proper organization is key to speeding up barcode scanning for inventory. Group similar items together and label storage areas clearly. This reduces the time spent searching for items and scanning barcodes. For example, one small shop saved 30 minutes per inventory check after reorganizing its layout and grouping related products.
3. Update Barcodes as Needed
Your barcode labeling for businesses should always reflect the current state of your inventory. When products are updated, discontinued, or repackaged, ensure their barcodes are refreshed. This prevents confusion during scanning and keeps your inventory system running smoothly.
4. Leverage Data for Smarter Decisions
Use the data generated by your inventory tracking for small business to forecast demand, identify trends, and prevent stockouts. For instance, you can analyze sales patterns to determine which products need to be reordered and which items may be overstocked. This insight allows you to manage stock levels more effectively and improve overall profitability.
By implementing these tips, you’ll not only simplify your small business barcode tracking but also improve the efficiency and accuracy of your inventory management practices.
Real-World Example: Barcode Tracking’s Impact on a Small Business
Let’s look at how barcode tracking transformed one business. Rohit runs a hardware store and often struggled with inventory issues—he’d over-order nails or run out of hammers at the worst times. Both Rohit and his customers were frustrated with the delays and inefficiencies.
That all changed when he adopted a barcode inventory system. With barcoding, he could track every product with a quick scan. His reorder process became effortless, and customer complaints dropped significantly. On top of that, Rohit saved hours each week on small business stock management. The result? A smoother operation, happier customers, and more time to focus on growing his business. If Rohit can do it, so can you!
How Barcode Technology Can Future-Proof Your Business
Barcode technology isn’t just a solution for today—it’s a stepping stone toward future innovations. By mastering small business inventory management with barcodes, you’re setting the stage for integrating advanced tools like RFID (Radio Frequency Identification) or IoT (Internet of Things) systems. These technologies can take your small business asset tracking to the next level by offering real-time data, predictive insights, and better connectivity across your operations.Start small with barcodes and gradually expand as your business grows. Over time, your automated inventory system can evolve into a fully connected operation, capable of handling the demands of tomorrow’s business landscape. Remember, barcoding is not just about solving today’s problems—it’s about future-proofing your business for continued success.
Conclusion: Own Your Inventory Right Now
Phew, we’ve covered a lot! You now have the roadmap to efficiently streamline your operations, from small business barcode tracking basics to implementing and running your barcode-based system. A barcode-based inventory system is more than just a tool — it’s a way to save time, reduce stress, and expand your business confidently. Whether it is about barcode inventory management or ramping up inventory tracking for your small businesses, the advantages are pretty evident.
Ready to take the leap? Begin looking for small business barcode solutions. Not sure where to begin? Look for AI-driven inventory solutions or talk to professionals to determine what’s right for your small business stock management. If only I had taken the time to scan! Your future self will thank you!
FAQs
What is the best barcoding inventory system for a small business?
The right barcode inventory system for you comes down to what you need and can afford. Companies such as OmneelabWMS are favorites for small business inventory management since they are low-cost and easy to use. Seek systems that allow barcode scanning for inventory and can work with your current back-end software.
How much does it cost to implement a barcode system for a small business?
Costs for implementing a barcode system differ. Simple setups with a handheld scanner and free software can be as little as $100-$200, while a more complex inventory management system with a printer and a subscription could cost $500 or more. It’s worth the investment for good small business stock tracking.
Can I track other small business assets with barcodes instead of just retail items?
Absolutely! Small business asset tracking with barcodes for your office, warehouse , or service-based business. Whether you are monitoring tools, equipment, or materials, barcoding in business can help keep track of valuable goods beyond the retail shelf.
How does barcode inventory control help small businesses?
Barcode stock management allows you to eliminate mistakes, make inventories a lot faster, and have instant information to improve your decisions. It’s a small business inventory management basic that prevents any loss of sale due to stock out or overstock.
How do you begin with the barcode system for inventory tracking?
To begin, consider what your small business inventory requirements are for inventory tracking. Then, invest in a scanner and barcode scanning software for inventory. Develop and implement barcodes with business barcode labeling, train staff, and proof barcode system output to successfully implement the barcode system.
People also read:
- Inventory Management with Barcode Technology
- Common Inventory Management Challenges
- Comprehensive Guide to Inventory Management Systems
- Manual and Automated Inventory Management
- Top 10 Tips for Warehouse Management Software
Kapil Pathak is a Senior Digital Marketing Executive with over four years of experience specializing in the logistics and supply chain industry. His expertise spans digital strategy, search engine optimization (SEO), search engine marketing (SEM), and multi-channel campaign management. He has a proven track record of developing initiatives that increase brand visibility, generate qualified leads, and drive growth for D2c & B2B technology companies.