In the world of supply chain and inventory management, maintaining accurate records and ensuring the seamless receipt of goods is critical. This is where the Goods Received Note (GRN) comes into play. Often overlooked but indispensable, the GRN is more than just a document—it’s the backbone of inventory accuracy, supplier accountability, and smooth business operations. Whether you’re managing a warehouse, running procurement for a retail chain, or overseeing a supply chain in a manufacturing setup, understanding the GRN process, its purpose, and its benefits is essential. In this article, we’ll explore everything you need to know about GRNs, including how they streamline operations, reduce errors, and ensure transparency in your supply chain.
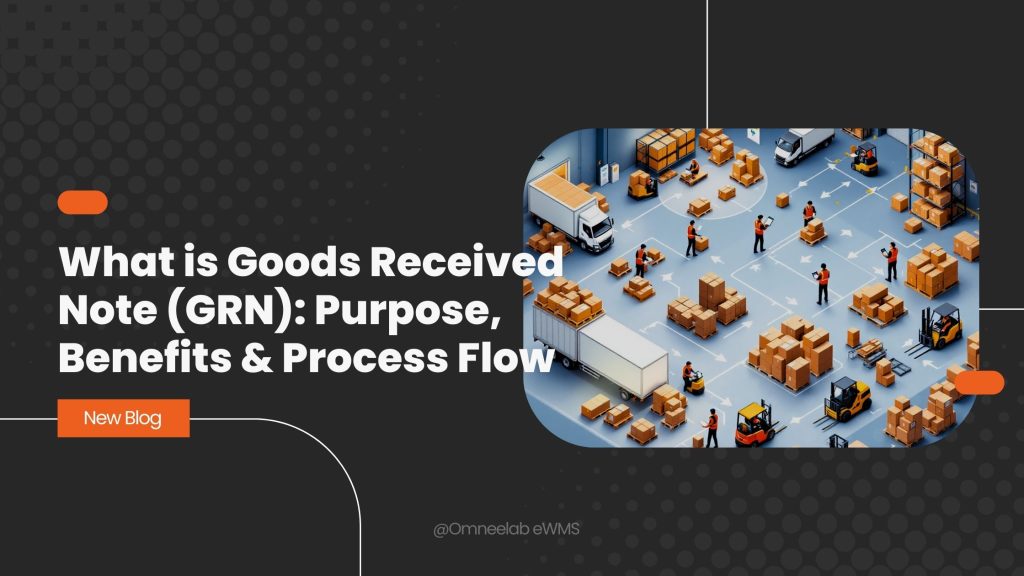
What is a Goods Received Note (GRN)?
A Goods Received Note (GRN) is a critical document in inventory and supply chain management. It is issued by the buyer’s warehouse or receiving team to confirm that the goods ordered from a supplier have been delivered in the correct quantity and quality. Acting as a bridge between suppliers and internal teams, the GRN ensures that the delivery aligns with the purchase order and highlights any discrepancies. A typical GRN includes:
- GRN number (unique identifier)
- Date of goods receipt
- Supplier details
- Purchase order (PO) reference
- Description of the goods
- Quantity received
- Remarks (e.g., damaged or missing items)
This document ensures effective communication between the procurement, inventory, and accounts departments while maintaining accurate records for future reference.
Importance of Goods Received Note (GRN) in Inventory Management
The purpose of a GRN extends beyond merely acknowledging the receipt of goods. It plays a vital role in maintaining operational efficiency, reducing errors, and enhancing supplier relationships. Let’s take a closer look at the key reasons why GRNs are essential:
1. Verification of Goods
A GRN ensures that the goods delivered by the supplier match the purchase order in terms of quantity, quality, and specifications. This prevents errors such as over-delivery, under-delivery, or defective items.
2. Accurate Inventory Tracking
By updating inventory records in real-time, a GRN ensures accurate buffer stock levels, helping businesses avoid issues like overstocking or stockouts.
3. Accounts Reconciliation
The GRN acts as a reference document for the accounts payable team to validate invoices submitted by suppliers. Payments are only processed for goods that have been received and verified.
4. Dispute Resolution
In the event of delivery discrepancies, the GRN serves as evidence during negotiations with suppliers, ensuring fair resolutions.
5. Audit and Compliance
The GRN creates a clear audit trail, which is essential for regulatory compliance and internal audits. It provides proof of delivery and receipt, ensuring transparency.
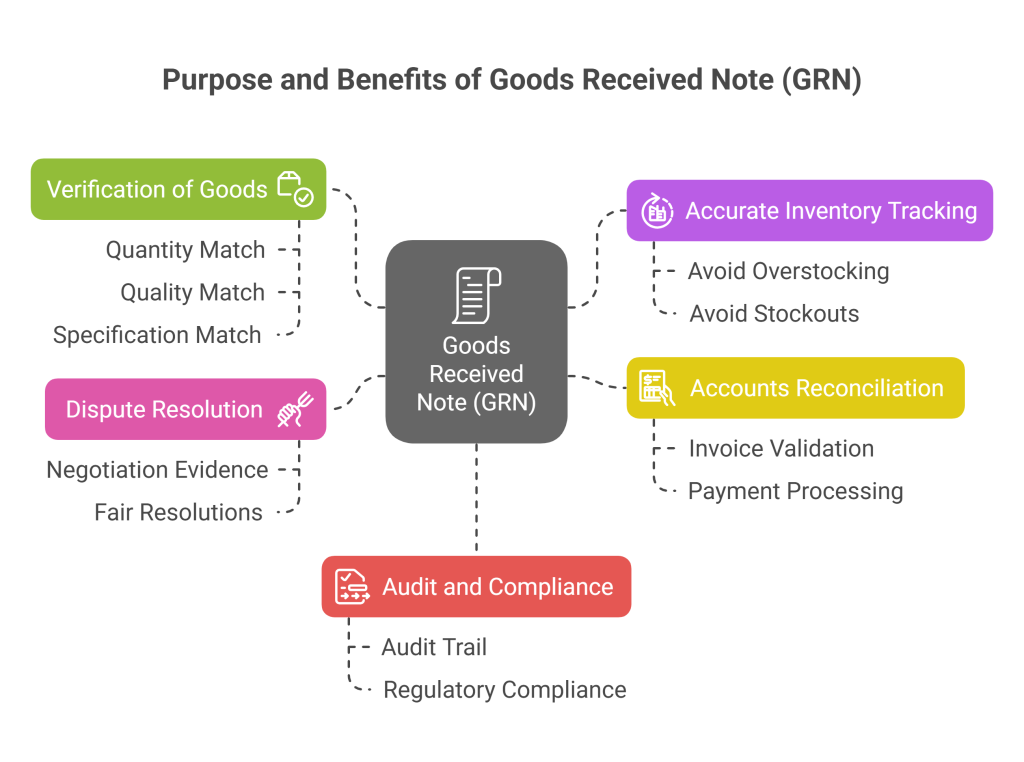
Benefits of an Efficient GRN Process
An efficient GRN process can significantly enhance your business operations. Here’s how:
1. Improved Accuracy in Inventory Management
By recording every detail of goods received, GRNs eliminate errors in stock levels and help maintain accurate inventory records.
2. Enhanced Supplier Accountability
Suppliers are held accountable for delivering goods as per the agreed terms, fostering trust and minimizing disputes.
3. Streamlined Procurement and Payment Cycles
The GRN bridges communication between procurement, inventory, and accounts payable teams, ensuring faster invoice processing and payment cycles.
4. Reduced Operational Costs
By identifying discrepancies early, businesses can avoid overpayments and unnecessary costs associated with returns or replacements.
5. Better Decision-Making
Real-time inventory updates from the GRN process enable better decision-making in procurement planning, stock replenishment, and supply chain optimization.
GRN Process Flow: Step-by-Step Guide
The GRN process flow is designed to ensure that goods are received, verified, and recorded accurately. Below is a step-by-step breakdown:
Step 1: Delivery of Goods
When goods arrive at the warehouse, the receiving team inspects the packages to verify the following:
- Quantity of items
- Quality and condition
- Alignment with the purchase order
Step 2: Creation of GRN
The receiving team creates a Goods Received Note using manual forms or digital systems. The GRN includes:
- Supplier name
- Delivery date
- Product details
- Quantity received
- Any remarks about damaged or missing goods
Step 3: Inventory Updates
Once the GRN is created, inventory records are updated to reflect the newly received stock. This ensures that stock levels remain accurate and up-to-date.
Step 4: Communication with Accounts Payable
The GRN is forwarded to the accounts department to validate supplier invoices. Payments are only made for items that are approved through the GRN.
Step 5: Filing and Documentation
The GRN is stored as part of the organization’s records for future reference, audits, and compliance requirements.
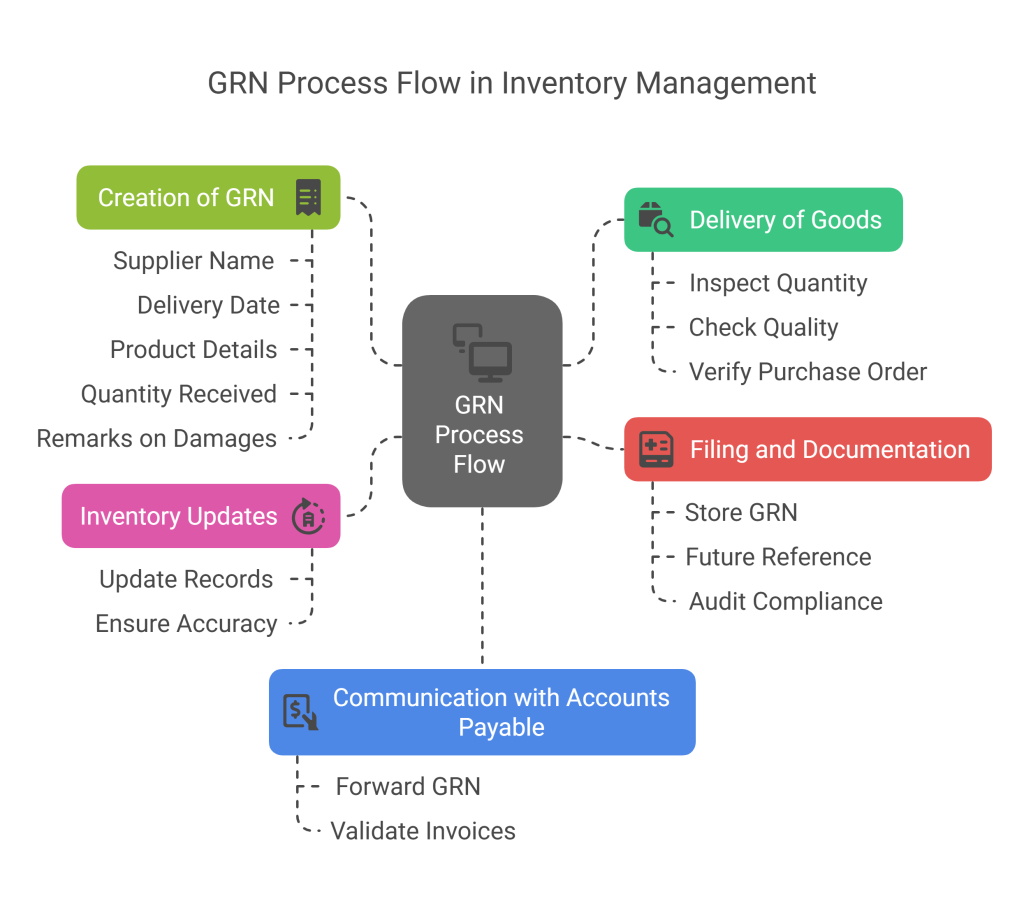
Challenges with Traditional GRN Processes
Traditional GRN processes, which rely on manual handling, pose several challenges:
1. Time-Consuming
Manually creating GRNs and updating inventory records can take a significant amount of time, especially for businesses handling large shipments.
2. Prone to Errors
Manual data entry increases the likelihood of mistakes, such as incorrect quantities or misfiled records.
3. Delayed Inventory Updates
Without real-time systems, stock levels are often updated with delays, leading to inaccurate inventory management.
4. Storage Issues
Paper-based GRNs require physical storage, which can be cumbersome and difficult to manage.
5. Limited Traceability
Tracking discrepancies or resolving disputes becomes challenging without digital records.
The Future of GRN: Digital and Automated Solutions
To overcome the challenges of traditional GRN processes, businesses are increasingly adopting digital solutions. Automated GRN systems streamline the process, reduce manual errors, and improve efficiency. Here’s how:
1. Real-Time Inventory Updates
Digital systems automatically update inventory levels as soon as the GRN is created, ensuring accurate stock records.
2. QR Codes for Tracking
Modern GRN systems generate QR codes for packages, enabling quick and error-free tracking using mobile apps.
3. Seamless ERP Integration
When integrated with ERP systems like SAP, Oracle, or Zoho, automated GRN systems sync data across procurement, inventory, and accounts modules.
4. Improved Visibility
Digital GRNs provide real-time visibility into goods received, enabling better decision-making and reducing bottlenecks in the supply chain.
5. Regulatory Compliance
Automated systems ensure that all GRN records are stored securely and can be retrieved easily during audits or inspections.
Why Businesses Should Prioritize an Efficient GRN Process
An efficient GRN process is not just about receiving goods—it’s about creating a seamless workflow that connects procurement, inventory, and accounts departments. By investing in automated GRN solutions, businesses can:
- Eliminate inefficiencies in manual processes
- Enhance supplier relationships
- Reduce operational costs
- Ensure compliance with regulatory standards
Final Thoughts
The Goods Received Note (GRN) is a cornerstone of effective supply chain and inventory management. From verifying goods and updating inventory to streamlining accounts payable, the GRN plays a pivotal role in ensuring operational efficiency and transparency. While traditional GRN processes have limitations, adopting digital solutions can revolutionize the way businesses manage goods receipt, making workflows faster, more accurate, and highly efficient. If you’re looking to optimize your GRN process, consider investing in an automated solution that integrates seamlessly with your ERP system. Streamlining your GRN process will not only improve inventory accuracy but also contribute to smoother operations and better financial management.
Start transforming your supply chain today with Omneelab WMS—because managing your goods receipt process shouldn’t be a hassle.
FAQs
A GRN is a document used in inventory and supply chain management to confirm that the goods received from a supplier match the purchase order in terms of quality and quantity.
A GRN ensures accurate inventory tracking, supplier accountability, and smooth accounts payable processes. It also serves as evidence in case of disputes or audits.
A GRN typically includes the GRN number, supplier details, delivery date, purchase order reference, product description, quantity received, and remarks on discrepancies.
Manual GRN processes are time-consuming, prone to errors, and lack real-time updates. They also require physical storage and limit traceability.
Businesses can improve their GRN process by adopting digital solutions with features like QR code integration, real-time inventory updates, and ERP system integration. By implementing these strategies, businesses can create a seamless and efficient GRN process that supports their overall supply chain and inventory management goals.
Kapil Pathak is a Senior Digital Marketing Executive with over four years of experience specializing in the logistics and supply chain industry. His expertise spans digital strategy, search engine optimization (SEO), search engine marketing (SEM), and multi-channel campaign management. He has a proven track record of developing initiatives that increase brand visibility, generate qualified leads, and drive growth for D2C & B2B technology companies.