Managing inventory efficiently is a cornerstone of any successful business that deals with products, warehousing, or supply chain operations. But how do you ensure that every team member follows the same process to keep your inventory accurate and organized? The answer lies in developing a Standard Operating Procedure for Inventory—or simply, an Inventory SOP.
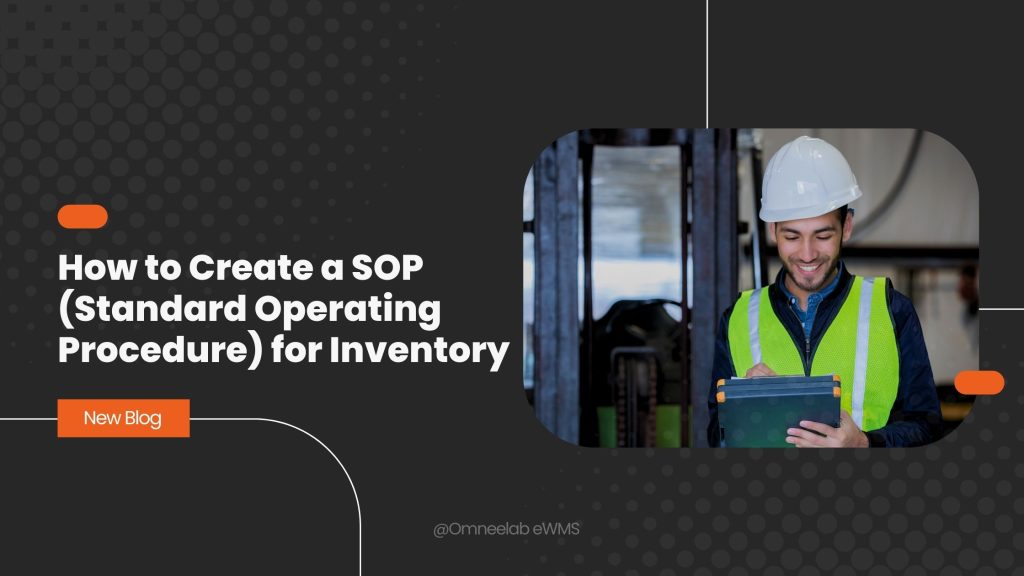
In this article, we’ll walk you through how to create an SOP for inventory that streamlines your inventory control process, enhances accountability, and supports consistent inventory documentation standards. Whether you’re just starting out or looking to improve your existing inventory management procedures, this guide covers everything from templates to workflow steps, sprinkled with practical tips and examples.
What is a Standard Operating Procedure for Inventory?
A Standard Operating Procedure for Inventory is a detailed document that outlines the exact steps employees must follow when managing inventory. It includes everything from receiving goods, tracking stock levels, handling returns, to performing inventory audits. The goal is to create a repeatable, standardized process that minimizes errors and maximizes efficiency.
Think of it like a recipe for your inventory management—everyone follows the same instructions, ensuring consistency no matter who is on duty.
Why You Need an SOP for Inventory
Have you ever experienced discrepancies between recorded and actual stock? Or dealt with lost or misplaced items in your warehouse? These are common challenges that highlight the importance of inventory process standardization.
Here are some compelling reasons to create an SOP for inventory:
- Reduces errors and inconsistencies in inventory tracking.
- Improves communication across teams by clarifying roles and responsibilities.
- Ensures compliance with industry standards and audit requirements.
- Speeds up training for new employees through clear guidelines.
- Supports better decision-making with accurate and timely inventory data.
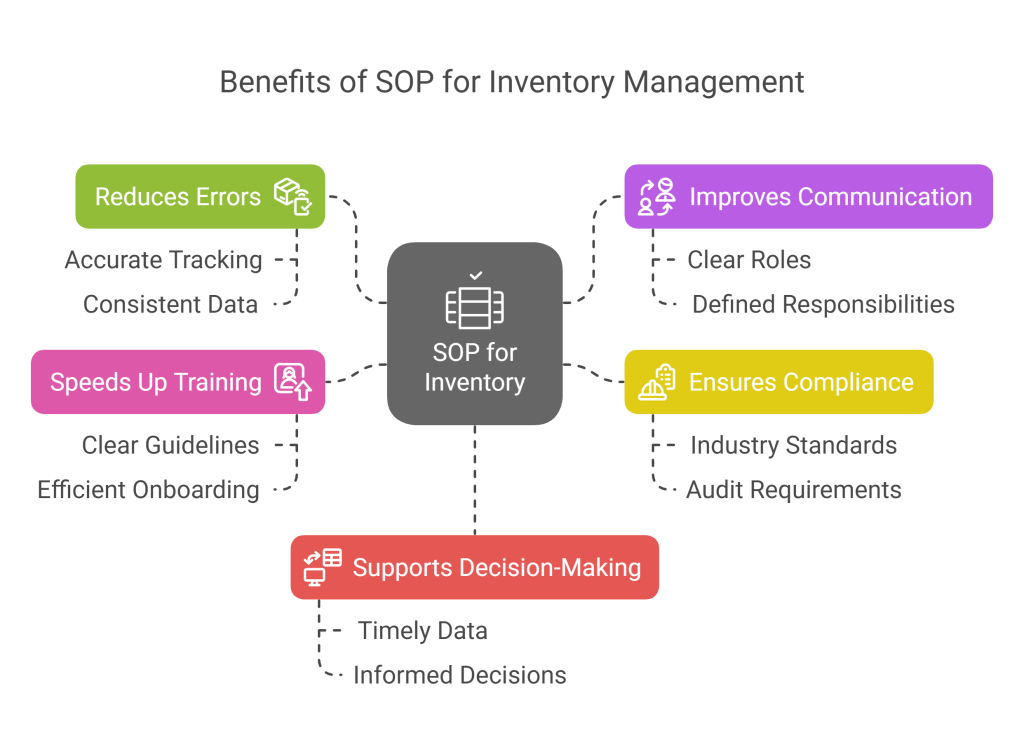
In short, an effective inventory SOP is your blueprint for flawless inventory management.
Step-by-Step Guide: How to Create an SOP for Inventory
1. Analyze Your Current Inventory Management Procedures
Before writing your SOP, take a close look at your existing inventory workflow. Identify:
- How inventory is received, stored, and issued.
- The tools or software used for inventory tracking.
- Any bottlenecks, inconsistencies, or pain points.
- Safety and handling instructions currently in place.
This analysis will help you understand what needs to be documented and improved.
2. Define the Scope and Objectives of Your SOP
Be clear about what your SOP will cover. For example:
- Receiving goods: Inspection and acceptance criteria.
- Inventory control process: How stock counts, transfers, and replenishments are handled.
- Inventory audit process: Frequency and method of stock reconciliation.
- Record keeping: Documentation standards and reporting.
Defining scope ensures your SOP stays focused and practical.
3. Choose an SOP Template for Inventory
Using a structured SOP template for inventory can simplify the writing process. A good template typically includes:
- Title and purpose of the SOP.
- Scope and applicability.
- Roles and responsibilities.
- Detailed step-by-step procedures.
- Safety and handling instructions.
- Glossary of terms (optional).
- Revision history.
You can find free sop templates below or customize one to fit your company’s needs.
4. Write Clear and Concise Inventory Workflow Steps
When writing SOP for inventory management, clarity is key. Use simple language and break down tasks into short, actionable steps. For example:
- Step 1: Verify the delivery against the purchase order.
- Step 2: Inspect the items for damage or discrepancies.
- Step 3: Log the received items in the inventory management system.
- Step 4: Store items in designated locations following handling instructions.
Use bullet points or numbered lists to enhance readability.
5. Incorporate Inventory Tracking Guidelines
Include detailed instructions on how to update inventory records, use barcodes or RFID scanners, and report discrepancies. This ensures everyone follows the same inventory tracking guidelines to maintain data accuracy.
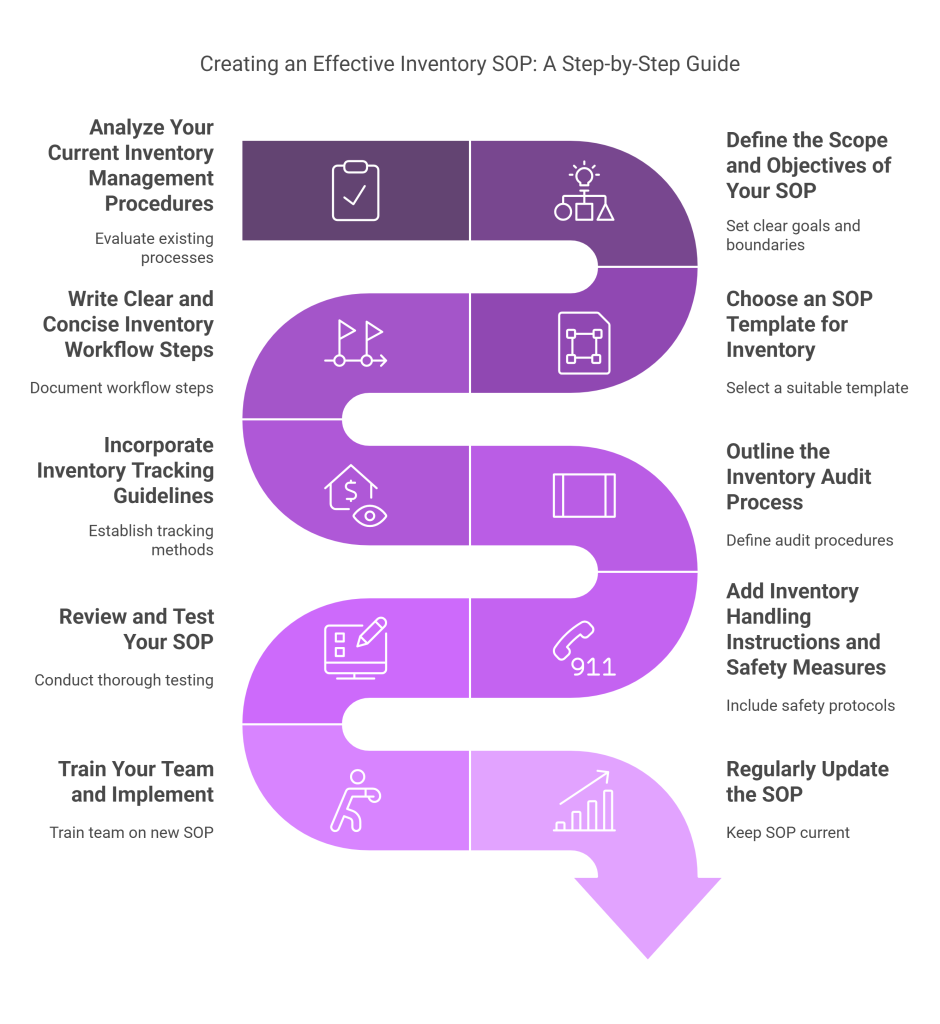
6. Outline the Inventory Audit Process
Regular audits are vital for inventory accuracy. Your SOP should specify:
- Audit schedule (monthly, quarterly, etc.).
- Methods (cycle counting, full physical inventory).
- Roles involved.
- How to document and resolve discrepancies.
7. Add Inventory Handling Instructions and Safety Measures
Inventory handling varies by product type. If you manage fragile, hazardous, or perishable goods, include specific instructions to prevent damage. Clear safety protocols protect employees and inventory alike.
8. Review and Test Your SOP
Before rolling out your new SOP, have team members review it for clarity and completeness. Conduct a trial run to identify gaps or confusion. This feedback loop helps fine-tune the procedure.
9. Train Your Team and Implement
Once finalized, train all relevant employees on the new SOP. Use hands-on demonstrations and provide access to the document for reference. Consistent training supports adherence to the inventory control process.
10. Regularly Update the SOP
Inventory practices and technologies evolve. Schedule periodic reviews to update your SOP, incorporating lessons learned and new best practices.
Tips for Effective Inventory SOPs
- Use simple language to avoid misunderstandings.
- Include visual aids like flowcharts or photos where possible.
- Keep paragraphs short and use bullet points for steps.
- Clearly define roles and responsibilities.
- Link your SOP to related documents, such as safety manuals or software guides.
Example: Simple SOP Template for Inventory
Section | Content Example |
---|---|
Title | Standard Operating Procedure for Inventory Management |
Purpose | To ensure consistent and accurate inventory control |
Scope | Applies to warehouse staff handling receipt, storage, and dispatch |
Roles | Warehouse Manager, Inventory Clerk, Quality Control Inspector |
Procedure | 1. Receive goods 2. Inspect items 3. Update inventory system 4. Store items |
Audit Process | Monthly cycle counts and discrepancy resolution |
Safety Instructions | Use gloves when handling fragile items; follow hazardous material protocols |
Revision History | Version 1.0 April 2025 |
Common Challenges in Inventory Management and How SOPs Help
Without a structured SOP, businesses often face:
- Stockouts or overstock situations.
- Lost or misplaced items.
- Inefficient warehouse operations.
- Inaccurate inventory data impacting decision-making.
An Inventory SOP addresses these challenges by providing clear inventory documentation standards and warehouse SOPs, which improve transparency and accountability.
Leveraging Technology to Enhance Your Inventory SOP
Modern inventory management systems can automate many tasks outlined in your SOP, such as scanning barcodes and real-time stock updates. Integrating technology with your SOP makes the inventory process more efficient and reduces human error.
Conclusion
Creating a Standard Operating Procedure for Inventory is essential for any business looking to improve accuracy, efficiency, and accountability in their inventory management. By carefully analyzing your current procedures, defining clear workflow steps, and incorporating best practices like the inventory audit process and inventory tracking guidelines, you set your team up for success.
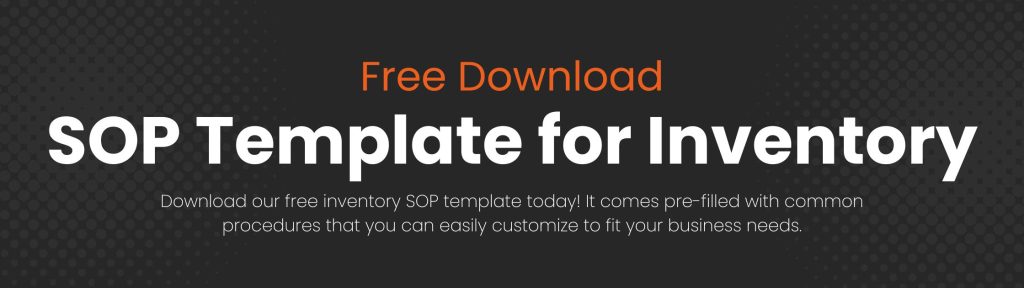
Remember, an SOP is a living document—keep it updated and train your staff regularly to maintain high standards.
Ready to take your inventory management to the next level? Explore AI-powered inventory tools like Omneelab eWMS to automate data entry, predict stock needs, and optimize workflows today!
FAQs
1. What is the difference between an SOP for inventory and general inventory management procedures?
An SOP for inventory is a detailed, step-by-step guide focused on standardizing specific tasks, while inventory management procedures encompass the broader strategies and policies used to handle inventory.
2. How often should I update my inventory SOP?
It’s best to review and update your SOP at least once a year or whenever there is a significant change in your inventory process or technology.
3. Can an SOP help with inventory audits?
Absolutely! An SOP outlines the inventory audit process, ensuring audits are conducted consistently and discrepancies are handled properly.
4. What are the key components of an effective inventory SOP?
Clear objectives, defined roles, detailed inventory workflow steps, safety instructions, and procedures for record keeping and audits.
5. How do warehouse SOPs relate to inventory SOPs?
Warehouse SOPs often include inventory SOPs as part of broader operational guidelines, covering storage, handling, and movement of goods to maintain accuracy and safety.
People also read:
- Choosing the Right Warehouse Management Solution
- Inventory Control: Types, Methods & Strategies
- Mastering Inventory Audits
- Inventory Management with Barcode Technology
- Common Inventory Management Challenges
Kapil Pathak is a Senior Digital Marketing Executive with over four years of experience specializing in the logistics and supply chain industry. His expertise spans digital strategy, search engine optimization (SEO), search engine marketing (SEM), and multi-channel campaign management. He has a proven track record of developing initiatives that increase brand visibility, generate qualified leads, and drive growth for D2C & B2B technology companies.