Introduction
In the dynamic and fast-paced world of Fast-Moving Consumer Goods (FMCG), efficient management of inventory plays a critical role in ensuring operational success. Among the many challenges FMCG companies face, the real-time problem of batch and expiry tracking stands out as a significant hurdle. Without the right systems in place, organizations risk product wastage, regulatory non-compliance, and, ultimately, customer dissatisfaction.
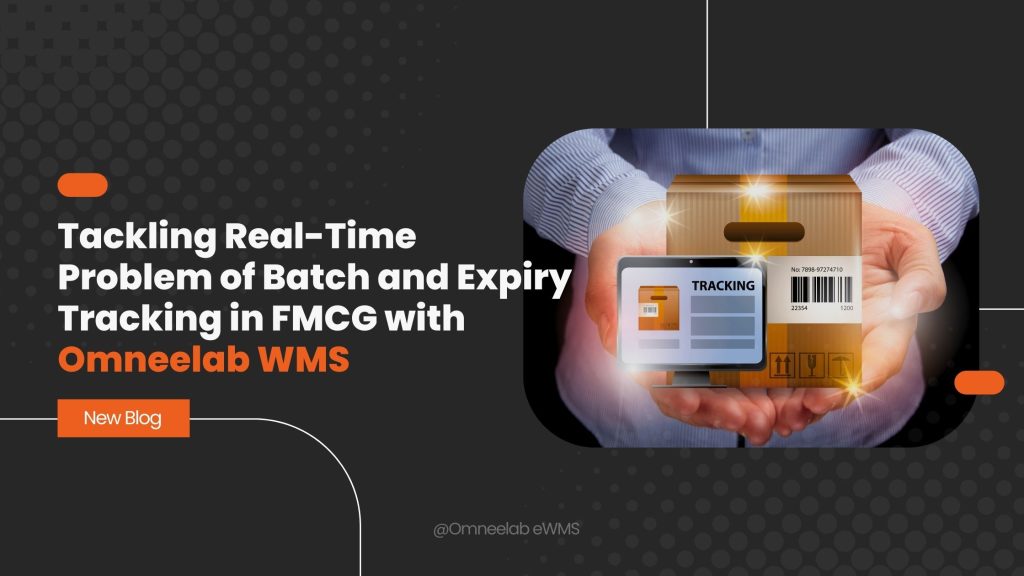
This is where Omneelab Warehouse Management System (WMS) comes into the picture. With its advanced features, Omneelab WMS provides real-time batch and expiry date tracking, ensuring that FMCG companies can optimize their inventory processes, maximize productivity, and maintain the highest standards of quality assurance.
In this article, we will explore the challenges of batch and expiry tracking in FMCG, how Omneelab WMS addresses these challenges, and why implementing such a system is essential for achieving operational excellence. Let’s dive in!
The Real-Time Problem in FMCG: Batch and Expiry Tracking
Understanding Batch and Expiry Tracking Challenges
For FMCG companies, tracking products by batch and monitoring their expiry dates is crucial for several reasons:
- Regulatory Compliance: Many countries have strict regulations regarding expired products. Companies must ensure no expired goods reach customers.
- Product Recalls: In case of a defective product, batch tracking allows companies to recall specific batches rather than the entire inventory.
- Customer Trust: Delivering expired or substandard goods can damage a company’s reputation and erode customer trust.
However, the sheer scale of inventory in the FMCG sector poses a unique challenge. Thousands of products, each with different batch numbers and expiry dates, need to be monitored in real-time. Traditional methods, such as manual tracking or outdated software, often result in errors, delays, and inefficiencies. This is the crux of the real-time problem in FMCG.
The Role of Omneelab WMS in Tackling Real-Time Challenges
Omneelab Warehouse Management System (WMS) is a comprehensive software platform developed to enhance warehouse operations through efficient inventory management and real-time tracking of batches and expiry dates. Designed with the needs of industries like FMCG in mind, it integrates advanced functionalities to address the complexities of modern supply chains.
Through the digitization and automation of processes, Omneelab WMS enables seamless tracking of products across their entire lifecycle—from production and storage to distribution and sale. This approach reduces reliance on manual methods, which are often prone to errors, and enhances visibility and accuracy in managing inventory. By implementing such a system, companies can ensure smoother operations and minimize inefficiencies that could otherwise disrupt the supply chain.
Key Features of Omneelab WMS for Batch and Expiry Tracking
Efficient batch and expiry tracking is a critical requirement for industries like FMCG, where product quality, compliance, and operational efficiency are paramount. Omneelab WMS incorporates several advanced features to address these needs, ensuring seamless inventory management and minimizing risks associated with manual tracking.
Real-Time Monitoring
Omneelab WMS provides comprehensive, real-time visibility into inventory across the supply chain. This feature allows businesses to monitor product batches and expiry dates as they move through various stages, from manufacturing to distribution. Real-time updates ensure that decision-makers have accurate and up-to-date information to act promptly.
Automated Alerts
The system is equipped with automated alert mechanisms that notify users when products are nearing their expiry dates. These alerts help prioritize the movement or sale of such products, reducing the risk of wastage and ensuring compliance with regulatory standards. This proactive approach minimizes losses and enhances inventory turnover.
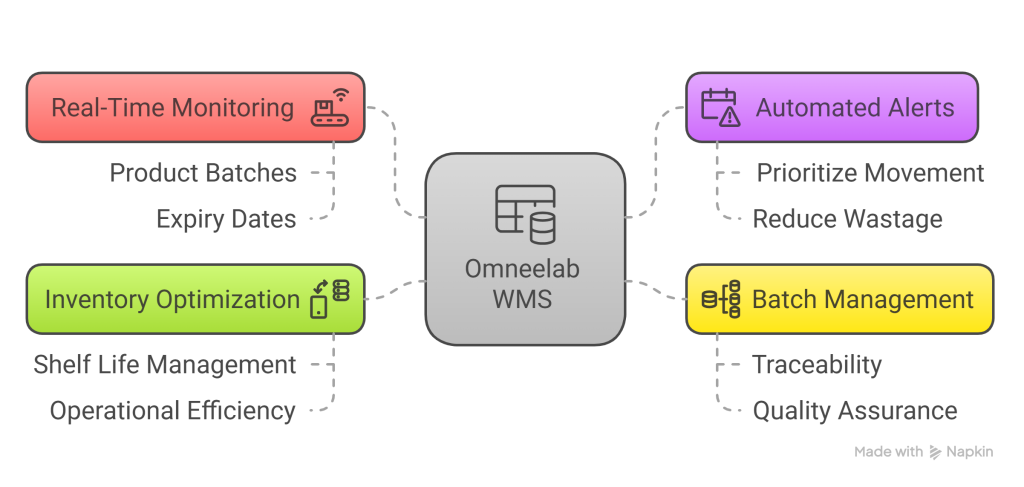
Batch Management
Each product batch is assigned a unique identifier within the system, enabling precise tracking throughout its lifecycle. This feature ensures traceability, which is essential for managing recalls, maintaining quality assurance, and adhering to industry regulations. Batch management also simplifies the process of identifying and isolating specific products when necessary.
Inventory Optimization
By integrating batch and expiry tracking with broader inventory management processes, Omneelab WMS helps businesses optimize storage and distribution. Products are managed based on their shelf life, ensuring that older inventory is prioritized for movement. This approach not only reduces wastage but also improves overall operational efficiency by aligning inventory management with business goals.
These features collectively address the complexities of batch and expiry tracking, providing businesses with the tools needed to maintain product quality, reduce inefficiencies, and meet compliance requirements.
Case Study: Explore the critical role of lubricants in ensuring operational efficiency in the oil and lubricant industry
Benefits of Using Omneelab WMS for FMCG Companies
Efficient warehouse management is critical for FMCG companies, where high product turnover, strict regulatory requirements, and the need for quality assurance demand robust systems. Implementing a Warehouse Management System (WMS) like Omneelab can address these challenges by streamlining operations and improving overall efficiency. Below are the key benefits of using Omneelab WMS in the FMCG sector:
Enhanced Operational Efficiency
Automating batch and expiry tracking significantly reduces the reliance on manual processes, which are often prone to errors and time-consuming. By leveraging real-time monitoring and automated workflows, Omneelab WMS enables businesses to streamline inventory management tasks. This allows companies to allocate resources more effectively and focus on strategic initiatives, such as optimizing supply chain performance or expanding market reach.
Improved Quality Assurance
Maintaining product quality is a top priority in the FMCG industry, where consumer trust and safety are paramount. Omneelab WMS ensures that products are tracked accurately throughout their lifecycle, from manufacturing to distribution. Real-time tracking and automated alerts help identify and isolate expired or defective batches before they reach consumers, reducing the risk of quality-related issues and ensuring compliance with industry standards.
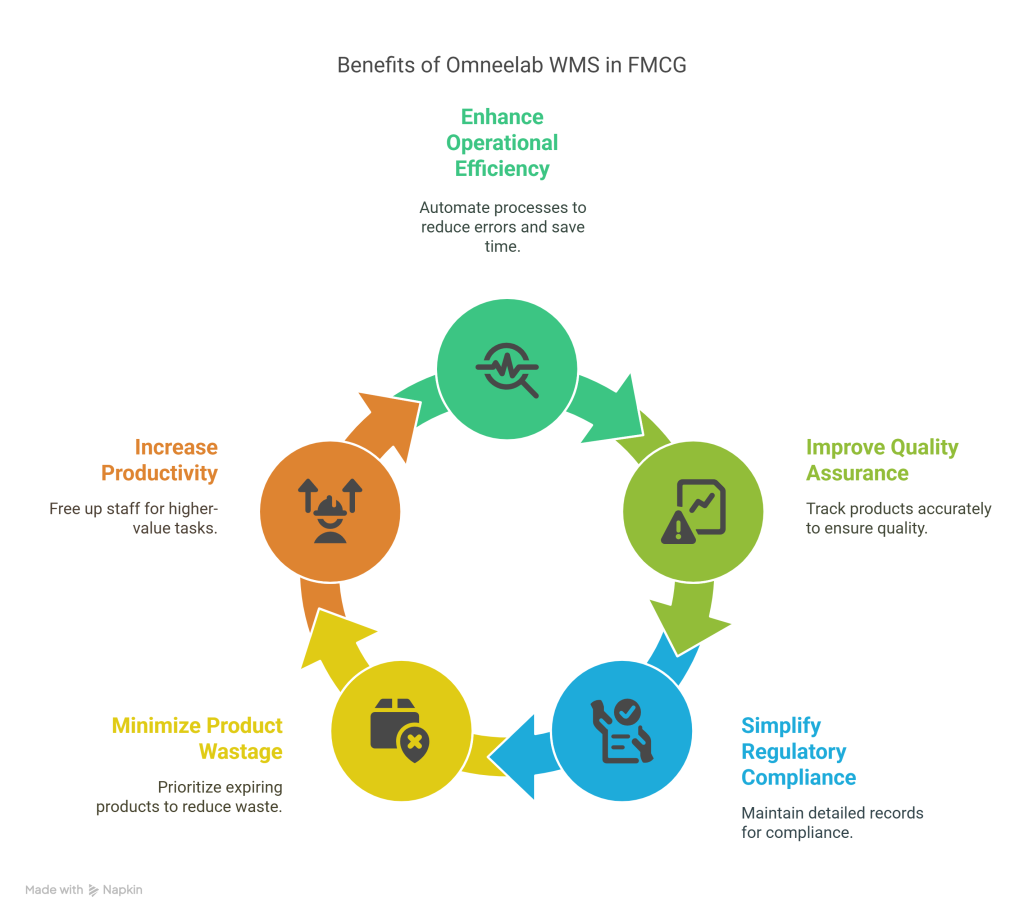
Simplified Regulatory Compliance
FMCG companies operate in a highly regulated environment, where maintaining detailed records of batch numbers, expiry dates, and product movements is essential. Omneelab WMS simplifies compliance by providing a centralized system for tracking and documenting inventory data. This ensures that businesses can meet regulatory requirements efficiently while maintaining a clear audit trail for inspections or recalls.
Minimized Product Wastage
One of the most significant challenges in FMCG is managing perishable goods and minimizing wastage due to expired stock. By prioritizing products nearing their expiry dates for sale or distribution, Omneelab WMS helps optimize inventory turnover. This proactive approach not only reduces financial losses but also supports sustainable business practices by minimizing waste.
Increased Productivity
With features like real-time monitoring, automated alerts, and batch tracking, Omneelab WMS reduces the workload on warehouse staff. Employees can focus on higher-value tasks, such as process optimization or customer service, while the system handles routine tracking and reporting. This results in improved productivity and better utilization of human resources.
How Omneelab WMS Adapts to Unpredictable Market Demands
Flexibility in Inventory Management
FMCG companies operate in a market that is constantly changing. Sudden shifts in consumer demand can lead to overstocking or understocking, both of which have serious consequences. Omneelab WMS provides real-time insights into inventory levels, enabling companies to respond quickly to changes in demand.
Leveraging Reinforcement Learning for Optimization
Omneelab WMS incorporates reinforcement learning, a type of artificial intelligence that enables the system to improve over time. By analyzing historical data and learning from past trends, the system can make smarter decisions about inventory allocation, product movement, and warehouse optimization.
The Connection Between Batch Management and Secondary Sales Data Tracking
In addition to tracking products within the warehouse, FMCG companies must also monitor their performance in the market. Secondary sales data tracking refers to the process of analyzing sales trends at the distributor and retailer levels. This data provides valuable insights into consumer preferences and market demand.
How Omneelab WMS Simplifies Secondary Sales Tracking
Omneelab WMS integrates batch tracking with secondary sales data, creating a seamless flow of information between warehouses and markets. This allows companies to:
- Identify which batches are performing well.
- Adjust production and distribution strategies based on sales trends.
- Ensure that products nearing expiry are prioritized for sale, even at the retail level.
Real-World Applications: Omneelab WMS in Action
The true value of any warehouse management system lies in its practical application and measurable results. To better understand the impact of Omneelab WMS, let’s delve into a real-world example of how it transformed operations for an FMCG manufacturer struggling with common challenges.
Case Study: FMCG Company X – Overcoming Batch and Expiry Challenges
Background:
Company X is a prominent FMCG manufacturer with a large product portfolio that includes cosmetics & pharmaceutical products. Due to rapid inventory turnover and the complexity of managing thousands of SKUs (stock-keeping units), the company faced significant difficulties in tracking product batches and expiry dates.
Before implementing Omneelab WMS, Company X relied on a semi-automated system and manual tracking methods, which led to inefficiencies, errors, and high wastage rates. Their inventory management challenges included:
- Excessive Product Wastage: Expired products were frequently discovered too late to be sold, leading to significant financial losses.
- Regulatory Compliance Issues: Inadequate batch tracking made it difficult to provide proper audit trails during inspections, increasing the risk of penalties.
- Labor Inefficiencies: Warehouse staff spent excessive time manually updating records and cross-checking inventory, reducing overall productivity.
Company X recognized the need for a more robust, automated solution to address these pain points. After evaluating various options, they implemented Omneelab WMS to streamline their batch and expiry tracking processes.
Implementation of Omneelab WMS
The implementation process was carried out in three key phases:
1. System Integration and Configuration:
Company X integrated Omneelab WMS with their existing ERP system to enable seamless data transfer. Omneelab WMS seamlessly integrates with ERP systems like SAP and Oracle, enabling real-time data synchronization across departments. Additionally, IoT-enabled sensors can be connected to monitor environmental conditions, such as temperature and humidity, for perishable goods.
According to industry reports by FICCI, FMCG companies lose approximately $260 billion annually due to expired or wasted products. Furthermore, nearly 60% of companies report challenges in managing batch and expiry tracking effectively, often due to reliance on outdated systems or manual processes. By implementing Omneelab WMS, Company X aimed to address these challenges and align their operations with industry best practices.
- Assigning unique batch identifiers to every product.
- Configuring automated alerts for products nearing their expiry dates.
- Mapping the warehouse layout in the system for real-time inventory tracking.
2. Staff Training and Process Optimization:
The warehouse team was trained to use Omneelab WMS effectively, focusing on the dashboard interface, real-time monitoring, and batch management tools. Manual processes such as paper-based tracking were replaced with barcode scanning and automated reporting to reduce human error.
3. Monitoring and Refinement:
Post-implementation, the company monitored key performance indicators (KPIs) such as inventory turnover, wastage rates, and compliance metrics. Adjustments were made to further optimize workflows based on the insights provided by Omneelab WMS’s analytics tools.
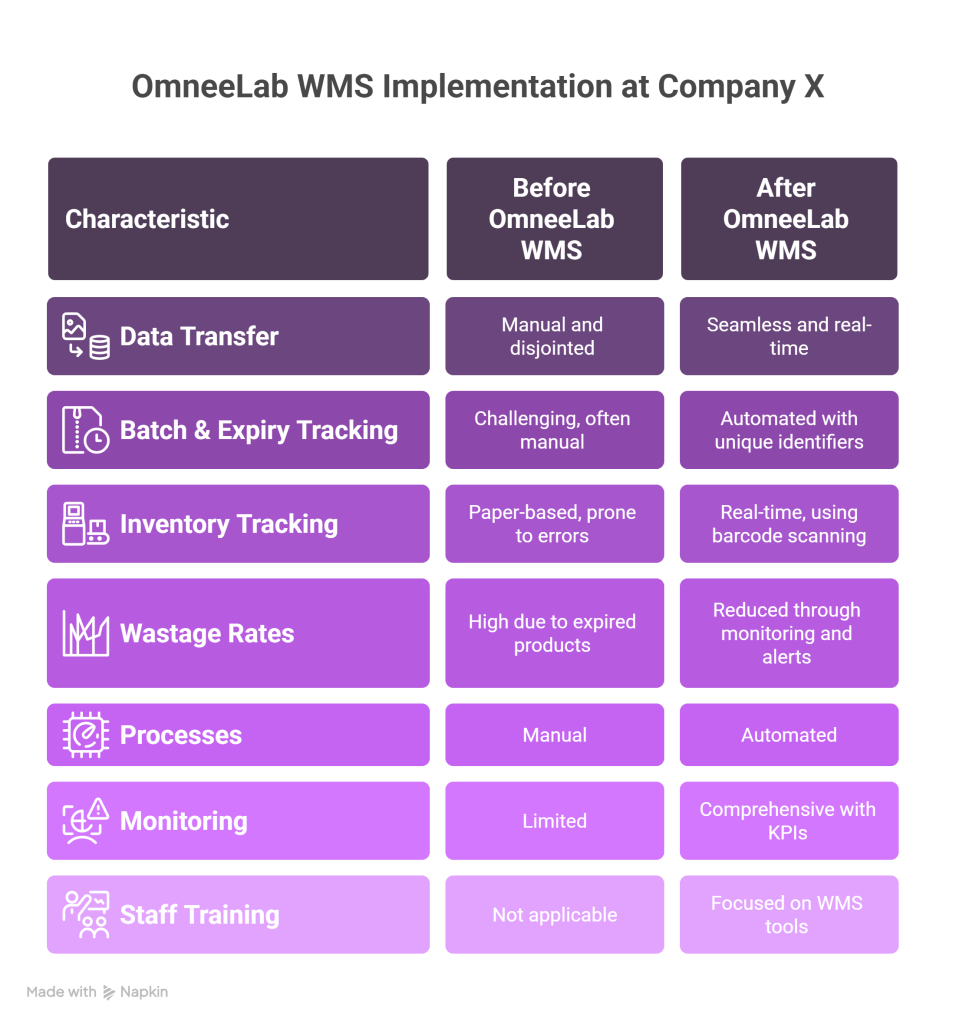
Results Achieved with Omneelab WMS
Within six months of implementation, Company X experienced measurable improvements across multiple areas of their operations:
1. 35% Reduction in Product Wastage
One of the most significant outcomes was the dramatic reduction in product wastage. Omneelab WMS’s automated alert system flagged batches nearing expiry, allowing the company to prioritize their sale or distribution. This proactive approach ensured that inventory was moved efficiently, minimizing the risk of expired products accumulating in the warehouse.
For example, a batch of cosmetics & pharmaceutical products that would have gone unnoticed previously was flagged by the system two weeks before expiry. The company responded by offering discounts to distributors, ensuring the products were sold before their shelf life ended.
2. 20% Increase in Productivity
With Omneelab WMS automating time-consuming tasks like batch tracking, expiry monitoring, and reporting, warehouse staff could focus on higher-value activities such as optimizing storage layouts and improving order fulfillment processes. This shift not only improved operational efficiency but also enhanced employee satisfaction by reducing repetitive, manual work.
Additionally, Omneelab’s barcode scanning feature sped up product handling significantly, reducing the time required to locate, track, or update batch information.
3. Improved Compliance and Audit Readiness
Regulatory compliance is a critical concern in the FMCG industry, especially when dealing with perishable goods. Prior to implementing Omneelab WMS, Company X struggled to produce comprehensive audit trails during inspections.
With the new system in place, all batch records, expiry dates, and product movements were meticulously logged and easily accessible. During a routine regulatory audit, the company was able to demonstrate complete traceability for every product batch, passing the inspection without any issues.
Key Takeaways from Company X’s Experience
The transformation at Company X highlights how a robust warehouse management system can address complex challenges in batch and expiry tracking. Their success was driven by:
- Automation: Eliminating manual processes reduced errors, improved accuracy, and saved time.
- Proactive Inventory Management: Real-time alerts and tracking allowed for better decision-making and minimized wastage.
- Operational Visibility: A centralized system provided complete transparency into inventory movements, enhancing compliance and traceability.
By leveraging the advanced features of Omneelab WMS, Company X not only overcame their operational hurdles but also set a foundation for sustained growth and efficiency in a competitive market.
Conclusion: The Future of Batch and Expiry Tracking in FMCG
The real-time problem of batch and expiry tracking is one of the most pressing challenges faced by FMCG companies. However, with advanced solutions like Omneelab WMS, businesses can overcome this challenge and unlock new levels of efficiency, compliance, and customer satisfaction.
As the FMCG industry continues to evolve, the importance of sophisticated systems like Omneelab WMS will only grow. Companies that invest in such technologies today will be well-positioned to thrive in an increasingly competitive market.
Now is the time to take action. Explore how Omneelab WMS can transform your warehouse operations and help you tackle the challenges of batch and expiry tracking with ease.
FAQs
Batch and expiry tracking involve monitoring products based on their production batch numbers and expiry dates. It is crucial in FMCG to ensure product quality, regulatory compliance, and customer safety.
Omneelab WMS provides real-time monitoring, automated alerts, and advanced batch management features. These tools ensure that products are tracked accurately throughout the supply chain, minimizing wastage and optimizing inventory.
Yes, Omneelab WMS is designed to adapt to changing market conditions. Its real-time insights and reinforcement learning capabilities enable companies to respond quickly to shifts in demand.
Omneelab WMS ensures quality assurance by tracking batches and expiry dates, removing expired or defective products, and maintaining detailed records for compliance and audits.
The main benefits include enhanced operational efficiency, improved quality assurance, minimized product wastage, regulatory compliance, and maximized productivity.
Efficient batch and expiry tracking is essential for operational success in the FMCG industry. By exploring modern warehouse management solutions like Omneelab WMS, businesses can address these challenges effectively and ensure long-term growth. To learn more about how advanced WMS systems can optimize your operations, visit our resources or book a call with industry experts.
People also read:
- Business Need of Warehouse Management System
- What Is a Bill of Materials (BOM)? Expert Guide & Tips
- Common Inventory Management Challenges
- Top WMS Integration Types and Benefits
- Inventory Control Types, Methods, and Strategies
- Strategies to Improve Inventory Turnover
- Future of Warehouse Management Trends 2025
Kapil Pathak is a Senior Digital Marketing Executive with over four years of experience specializing in the logistics and supply chain industry. His expertise spans digital strategy, search engine optimization (SEO), search engine marketing (SEM), and multi-channel campaign management. He has a proven track record of developing initiatives that increase brand visibility, generate qualified leads, and drive growth for D2c & B2B technology companies.