In the world of inventory management, one concept stands out as crucial to maintaining smooth business operations: the Reorder Point (ROP). Whether you’re managing a small retail shop or a large supply chain, knowing when to reorder stock is essential to avoid stockouts, reduce costs, and ensure customer satisfaction. This article will cover everything you need to know about reorder points, including their definition, the reorder point formula, and why they are critical for businesses.
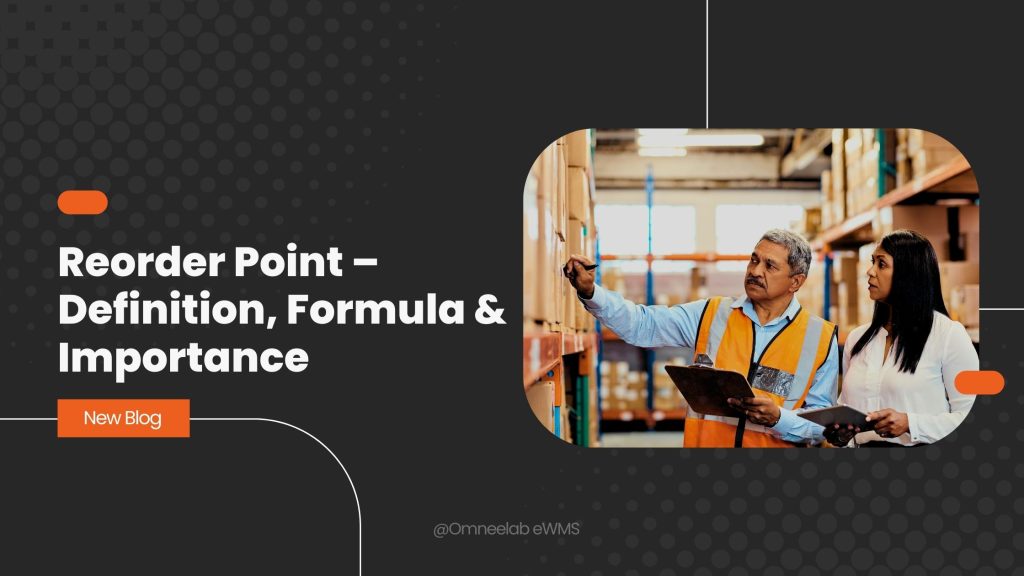
What Is a Reorder Point (ROP)?
The reorder point (ROP) is the minimum inventory level at which a business must initiate a replenishment order to avoid disruptions in operations. It’s essentially the stock level that triggers a restocking signal, ensuring you never run out of inventory while still optimizing storage costs.
Think of it as a safety net: when your inventory levels drop to a certain point, it’s time to reorder stock. Without a proper ROP in place, businesses risk stockouts, delayed deliveries, and dissatisfied customers.
Why Is the Reorder Point Important?
An effective reorder point is vital for maintaining optimal inventory levels while balancing costs and meeting customer demand. Here are a few reasons why businesses rely on ROP:
- Prevents Stockouts: Reorder points help businesses avoid running out of stock, ensuring customer orders are fulfilled on time.
- Optimizes Inventory Costs: By keeping stock levels at an optimal threshold, businesses avoid overstocking and reduce storage costs.
- Improves Supply Chain Efficiency: Knowing when to place a replenishment order allows for seamless coordination with suppliers, reducing delays.
- Enhances Inventory Control: ROP is a key component of inventory tracking, ensuring greater accuracy in stock management.
- Supports Business Operations Efficiency: Proper logistics planning and timely restocking ensure smooth business operations without unnecessary disruptions.
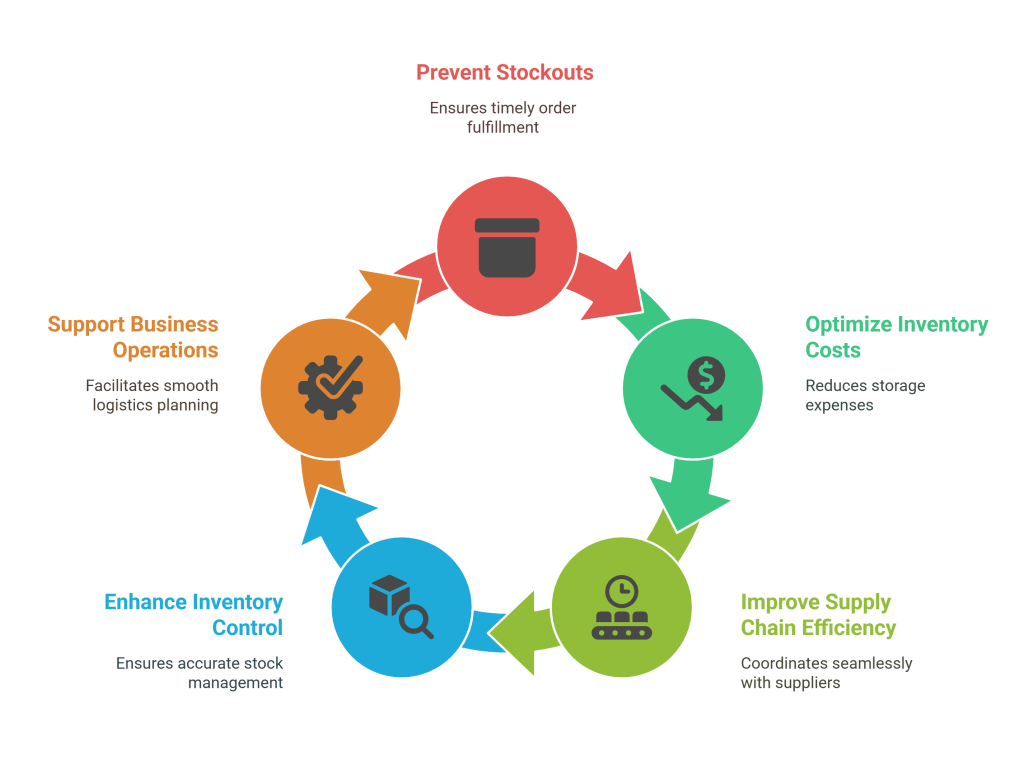
The Reorder Point Formula: How to Calculate ROP
Calculating the reorder point is straightforward, but it requires understanding a few key variables: lead time, safety stock, and average daily usage rate. Here’s the formula:
Reorder Point Formula:
Reorder Point (ROP) = (Average Daily Usage Rate × Lead Time) + Safety Stock
Let’s break this down:
- Average Daily Usage Rate: The average quantity of stock used or sold per day.
- Lead Time: The time (in days) it takes for a replenishment order to arrive after being placed.
- Safety Stock: An additional buffer stock kept on hand to account for unexpected demand or delays in the supply chain.
Example of Reorder Point Calculation
Imagine a business sells 50 units of a product daily (average daily usage rate). It takes 7 days for their supplier to deliver a replenishment order (lead time). To prevent stockouts, the business keeps 100 units of safety stock.
Using the formula:
Reorder Point (ROP) = (50 × 7) + 100 Reorder Point (ROP) = 350 + 100 Reorder Point (ROP) = 450
This means the business should reorder stock when their inventory falls to 450 units.
Factors That Influence the Reorder Point
Several factors impact the calculation and effectiveness of the reorder point. These include:
- Demand Patterns: Fluctuations in customer demand can affect the accuracy of your ROP. Seasonal changes, market trends, and promotions should be considered when calculating.
- Lead Time Variability: If supplier lead times vary, businesses may need to adjust their safety stock levels to accommodate delays.
- Inventory Turnover: High turnover rates may require more frequent reorders, while low turnover rates might allow for longer intervals between replenishments.
- Inventory Costs: Balancing the cost of holding stock with the risk of stockouts is crucial for maintaining profitability.
- Supply Chain Reliability: A dependable supply chain reduces the need for excessive safety stock, enabling more precise ROP calculations.
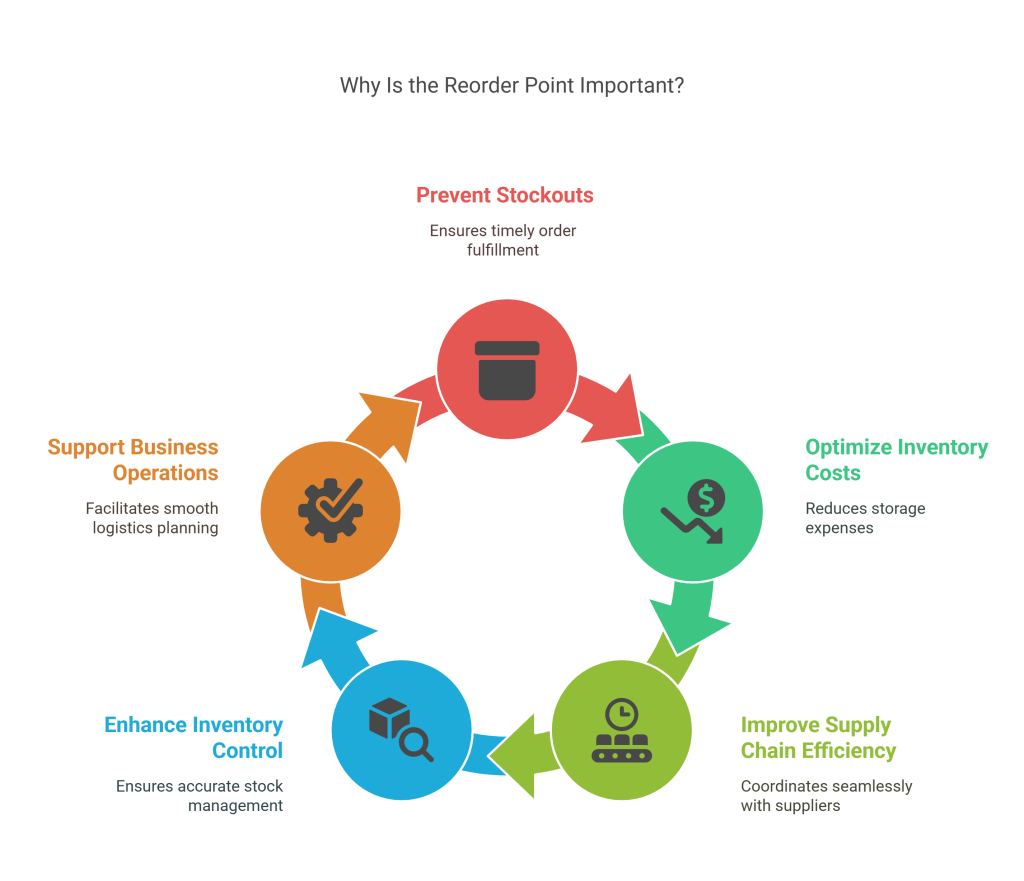
The Role of Reorder Points in Inventory Management
Reorder points are a cornerstone of inventory management. They help businesses maintain the right balance between minimum inventory levels and customer demand, ensuring operations remain efficient and cost-effective. Here’s how ROP contributes to effective inventory control:
- Stockouts Prevention: By acting as a restocking signal, ROP ensures businesses reorder stock before inventory runs out.
- Inventory Optimization: Helps businesses maintain the right amount of stock, avoiding overstocking or understocking.
- Improved Supply Chain Management: Knowing your reorder point allows for better coordination with suppliers, reducing delays and inefficiencies.
- Enhanced Business Operations Efficiency: Fewer disruptions in stock availability lead to smoother operations and happier customers.
Best Practices for Setting Reorder Points
To make the most of your reorder points, follow these best practices:
- Monitor Demand Trends: Keep an eye on historical sales data and demand patterns to identify fluctuations and predict future needs.
- Adjust for Lead Time Variability: Work closely with suppliers to understand their lead times and account for any inconsistencies in your ROP calculation.
- Incorporate Safety Stock: Always include a buffer to handle unexpected demand spikes or supply chain delays.
- Leverage Technology: Use inventory management software for inventory tracking and to automate ROP calculations.
- Review Regularly: Reevaluate your reorder points periodically to ensure they still align with your business needs and market conditions.
Common Mistakes to Avoid
While implementing reorder points can significantly enhance inventory control, there are a few pitfalls to watch out for:
- Ignoring Variability in Demand: Failing to account for seasonal or unexpected demand changes can lead to stockouts or overstocking.
- Over-Reliance on Safety Stock: While safety stock is essential, excessive reliance can inflate holding costs unnecessarily.
- Inaccurate Lead Time Assumptions: Misjudging supplier lead times can disrupt replenishment schedules.
- Not Using Technology: Manual tracking of ROP can be error-prone and inefficient. Invest in inventory management software for better accuracy.
- Failing to Regularly Update ROP: Changes in demand, supplier performance, or business operations require periodic recalibration of your reorder points.
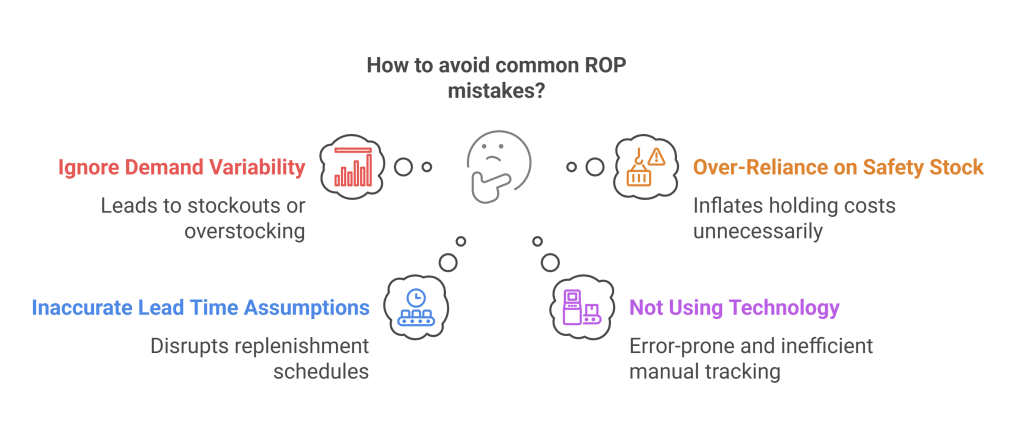
How Technology Enhances ROP
Modern businesses are increasingly leveraging technology to optimize their reorder points. Tools like AI-powered inventory optimization software provide real-time insights into stock levels, demand patterns, and supplier performance. Here’s how technology can improve your ROP strategy:
- Automated Calculations: Software can automatically calculate ROP based on real-time data, eliminating manual errors.
- Demand Forecasting: Advanced algorithms analyze historical data to predict future demand, ensuring more accurate ROPs.
- Inventory Tracking: Track stock levels across multiple locations to make informed replenishment decisions.
- Supply Chain Integration: Seamlessly integrate with suppliers to streamline the replenishment process.
Conclusion
The reorder point (ROP) is more than just a number—it’s a vital part of inventory management that ensures your business operates smoothly, efficiently, and profitably. By understanding the reorder point formula, considering critical factors like safety stock and lead time, and following best practices, businesses can avoid stockouts, reduce costs, and optimize their inventory.
It’s crucial to stay proactive. Regularly review and adjust your ROP as your business grows and market dynamics shift. Additionally, consider leveraging AI-powered tools to enhance your inventory control and streamline your supply chain management.
Are you ready to take your inventory management to the next level? Explore AI tools and inventory management solutions designed to optimize your business operations and boost efficiency.
FAQs About Reorder Points
The reorder point (ROP) is the inventory level at which a business must place a new order to replenish stock and avoid running out of inventory.
Use the formula:
Reorder Point (ROP) = (Average Daily Usage Rate × Lead Time) + Safety Stock
Safety stock acts as a buffer to accommodate unexpected demand spikes or delays in supply chain deliveries, ensuring stockouts are avoided.
AI-powered inventory management tools can automate ROP calculations, analyze demand patterns, and provide real-time insights for better decision-making.
A low ROP can lead to stockouts and missed sales opportunities, while a high ROP may result in excessive inventory costs and overstocking.
Kapil Pathak is a Senior Digital Marketing Executive with over four years of experience specializing in the logistics and supply chain industry. His expertise spans digital strategy, search engine optimization (SEO), search engine marketing (SEM), and multi-channel campaign management. He has a proven track record of developing initiatives that increase brand visibility, generate qualified leads, and drive growth for D2C & B2B technology companies.